
Throughout the project lifecycle, VDL Pinnacle Engineering focuses on inventing and implementing new ideas while creating systems for automotive OEMs and suppliers, as well as striving towards smart green factories that reduce environmental impact, writes Rajesh Rajgor following an exclusive interview with Dushyant Habbu, CEO, VDL Pinnacle Engineering India (P) Ltd.
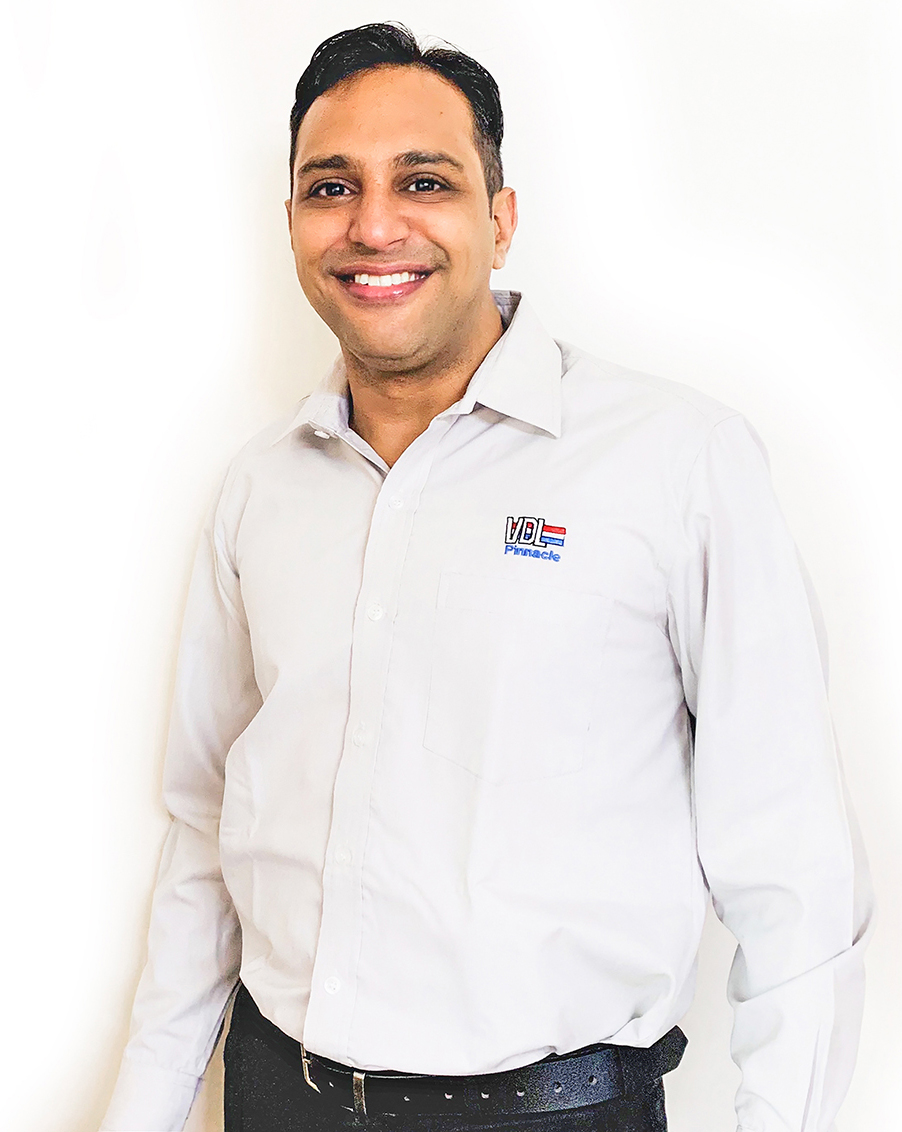
VDL Pinnacle Engineering is a joint venture between The Netherland’s VDL Group and India’s Pinnacle Industries. VDL Pinnacle Engineering began their operation in India in Pune, Maharashtra, in early 2016. Dushyant Habbu, CEO, VDL Pinnacle Engineering India, elaborates: “Starting out as a design and engineering firm to support the VDL Group’s engineering needs, we have evolved into a turnkey production systems provider for the automotive industry, while also supporting the VDL Group’s global offices and projects with design of production automation systems, body-in-white (BIW) tooling lines and bus and coach product design.”
VDL’s services include design, engineering and simulation to produce automotive fixtures and tooling and automation designs for a variety of medium-sized businesses in India and around the world. “We began as a design house, performing simulations, providing 3D drawings, 2D details, and other services to VDL Steelweld in the United Kingdom, the United States and The Netherlands. Given the low manual intervention in these countries, the focus of these initiatives was on updated fixtures and tooling for automobile production and assembly lines. Using robots, it was mostly about constructing a semiautomatic or fully automated line. From concurrent engineering to process definition, design, manufacture, assembly, installation, and commissioning to optimisation and training, we have got everything covered,” reveals Habbu.
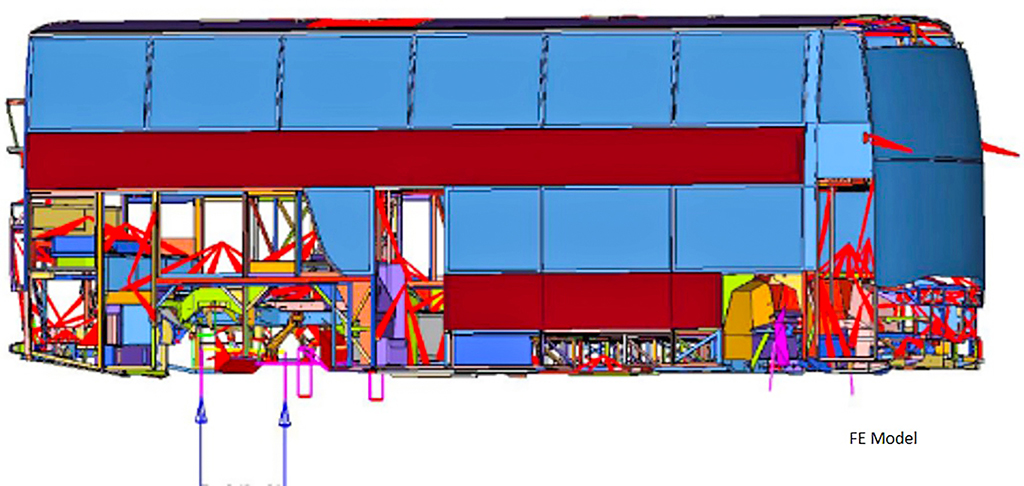
Designing a Product
VDL Pinnacle’s product design vertical, which is a branch of VDL Bus and Coach, develops solutions for the bus sector. VDL Pinnacle has also undertaken new bus designs based on existing bus designs, providing engineering solutions to improve working ergonomics of OEMs. “Out of the many solutions we provide for the bus business, FEA is one of the most important components. Various forms of analysis are carried out and the resultant reports can be used to make changes in the impacted region. Any model change necessitated by changes in emission regulations, such as the conversion from BS-VI to hybrid or hybrid to completely electric, has been handled by our staff,” informs Habbu.
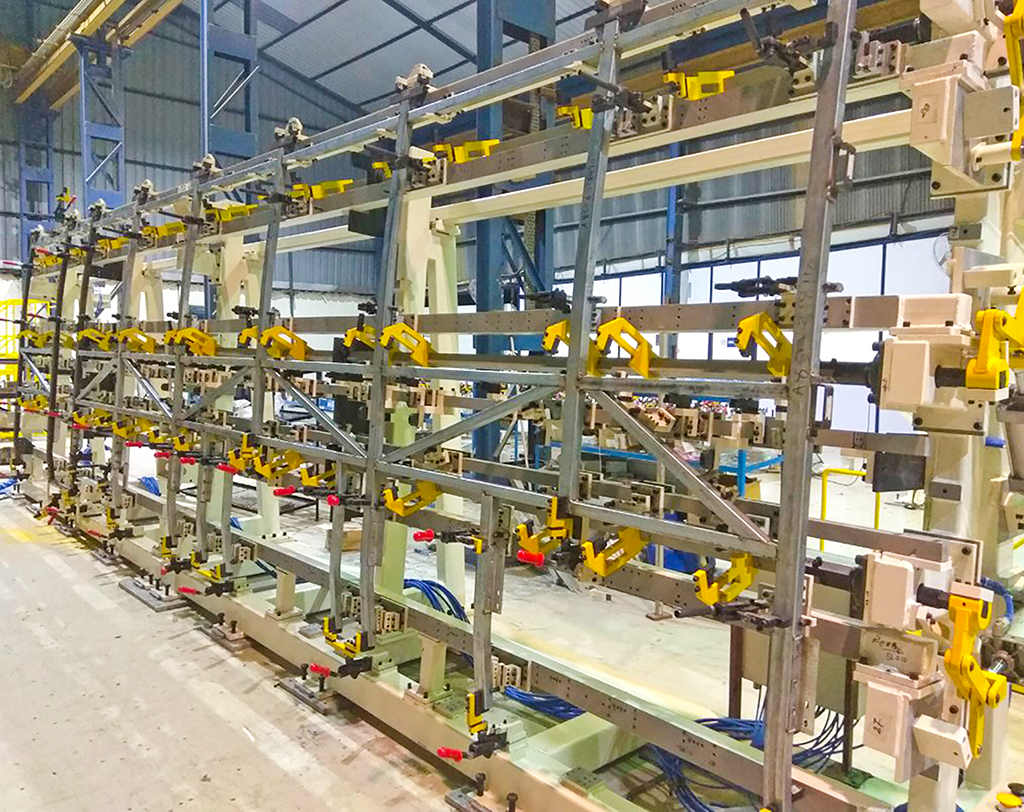
For one of the major OEMs, having its base in Chennai, VDL Pinnacle completed tooling for their nine-metre bus. “We delivered the fixtures for the under-frame, the front frame, the body side frame, the roof and the rear frame. So essentially the complete tooling for the bus was 100% designed, developed, manufactured and installed by VDL Pinnacle Engineering India,” Habbu points out. It was certainly tough for all the entities involved in public transport as soon as the pandemic hit. During such a time the engineers adapted to the changing needs of the OEMs. “The design engineers at these automotive OEMs came up with different concept. For instance, having bucket seats where you have these individual seats with minimum contact between people. Our design team did adapt with the new tooling and suppliers available. Similarly, the move to electric mobility fares well for our future. Not only do we have orders with two OEMs, but also having supplied to premium customers puts us at a decent enough level to capitalise on the earlier as well as upcoming orders. We are sure that there will be recovery of the segment in the next two years,” Habbu states.
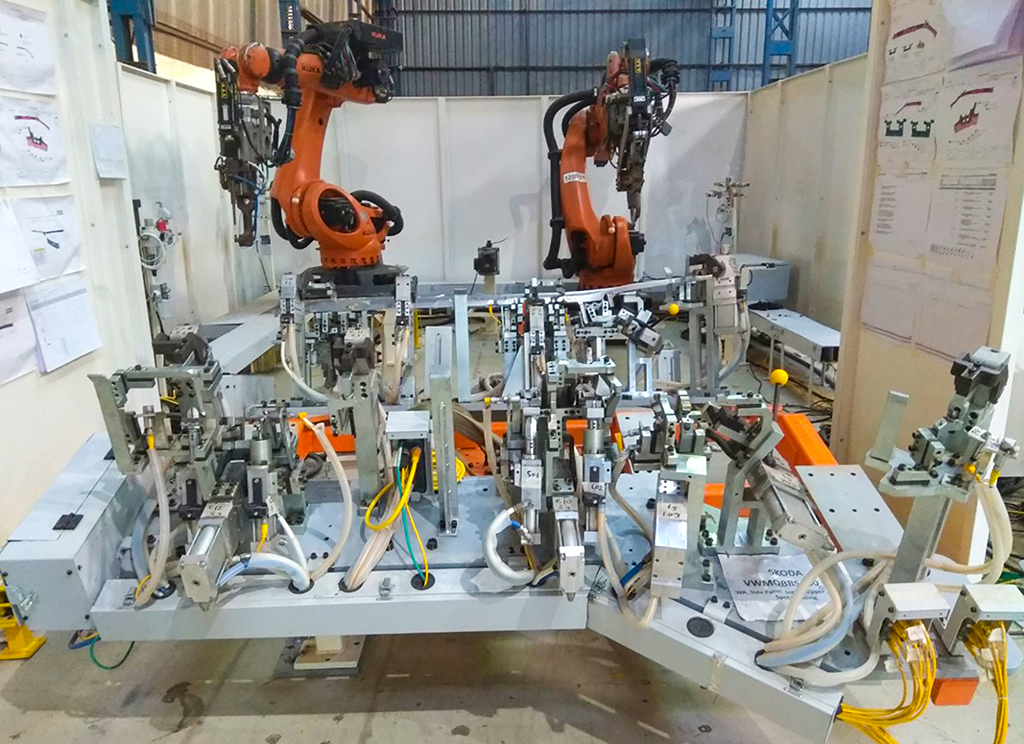
Towards Virtual Commissioning
VDL Pinnacle India has also brought a lot of new technologies to the country. They were the first to develop virtual commissioning. Virtual commissioning is the practice of using 3D technology to create a simulation model of a manufacturing facility so that planned changes and upgrades can be tested before they are implemented in the real plant. “One of the technologies that has never been deployed in India is a staple business for VDL Netherlands and these fitting lines where the vehicle’s doors, front left, right, bonnet and roof are all automatically mounted on the BIW body of the vehicle. This is something absolutely fresh for India. It hasn’t been applied anywhere, not even in the most prestigious automobile markets,” Habbu discloses.
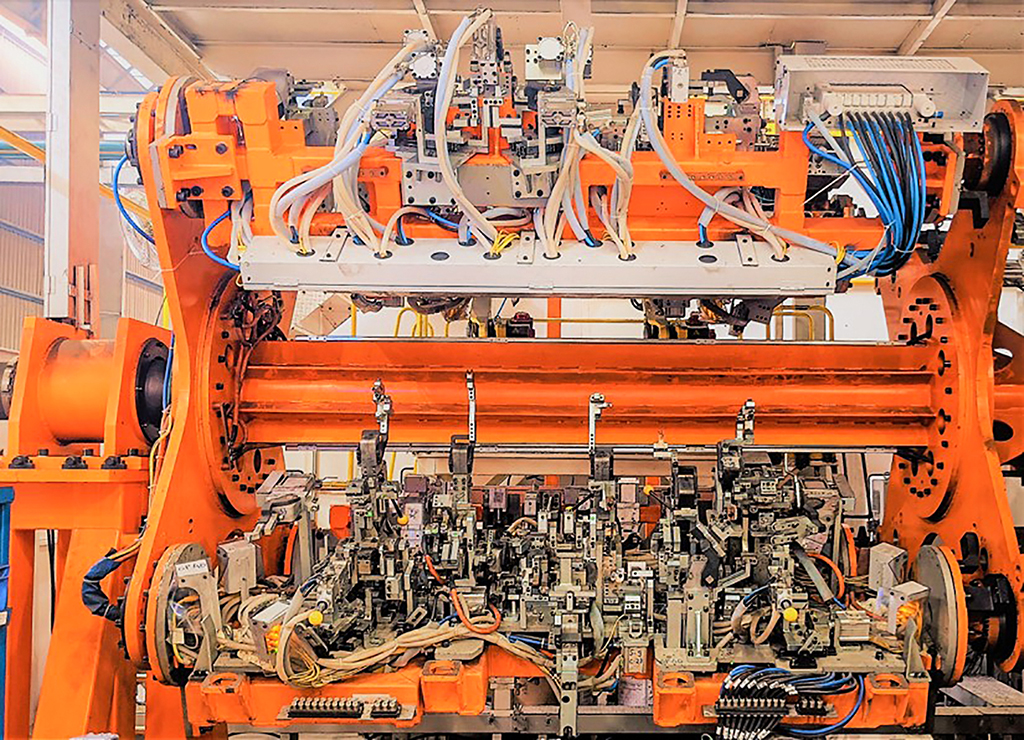
The traditional method was to finish the design, then ensure the production, and then add the electrical, control and automation parts. Later, trials are carried out, modifications are made, and the product is then shipped to the customer for eventual manufacturing at the OEM’s facility. The whole process took about 9-12 months. “Virtual commissioning brings in automation and electrical controls and the testing is immediately after the design phase where everything is software-based. This reduces a lot of time which is otherwise utilised in final commissioning at the customer site. So effectively it becomes a plug-and-play system,” Habbu states.
Design and Quality
Design and engineering are the most important aspects of any project. This is one of VDL Pinnacle’s most powerful packages. “Our engineers have been meticulously trained on worldwide design standards of all major OEMs, having spent 3+ years entirely in design services before starting full-fledged operations. Since its debut in April 2016, our team has successfully supplied concepts totalling about 1,00,000 hours,” says Habbu. Designs and quality of the design change as per the customers’ changing expectations. The mileage and the initial investment are what everyone concentrates on while buying a vehicle. VDL Pinnacle keeps track of these expectations and ensures changes are accommodated to give a more comfortable feel to the end users.
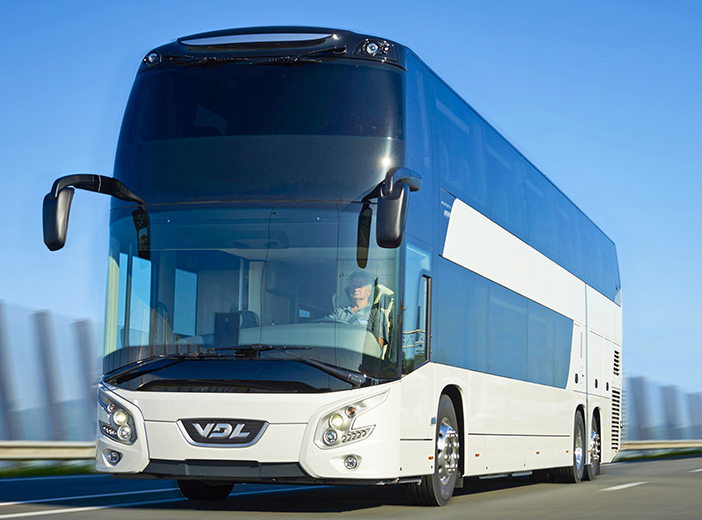
“In terms of manufacturability of the BIW, there are different materials but for us as a tooling line manufacturer, given some constraints that we have, customers expect durability of the fixtures, less maintenance, ergonomic use of the tooling and less fatigue for the operators. Of course, the price drives everything but usually we use MS material as it is durable. It not only lasts till the end of the production model for an OEM, but can also be modified for new models with a minor modification in the tools,” informs Habbu.
Growth beyond Vehicles
It is evident that the prime customers for VDL Pinnacle are the OEMs. However, as a lot of Tier I suppliers are going into complete automation owing to high volume of production, VDL Pinnacle can leverage its OE experience towards them. “We have already ventured into assisting Pinnacle Industries in their business of seat manufacturing. Our expertise in welding fixtures, assembly fixtures, inspection gauges is a good asset for our in-house companies,” reveals Habbu.
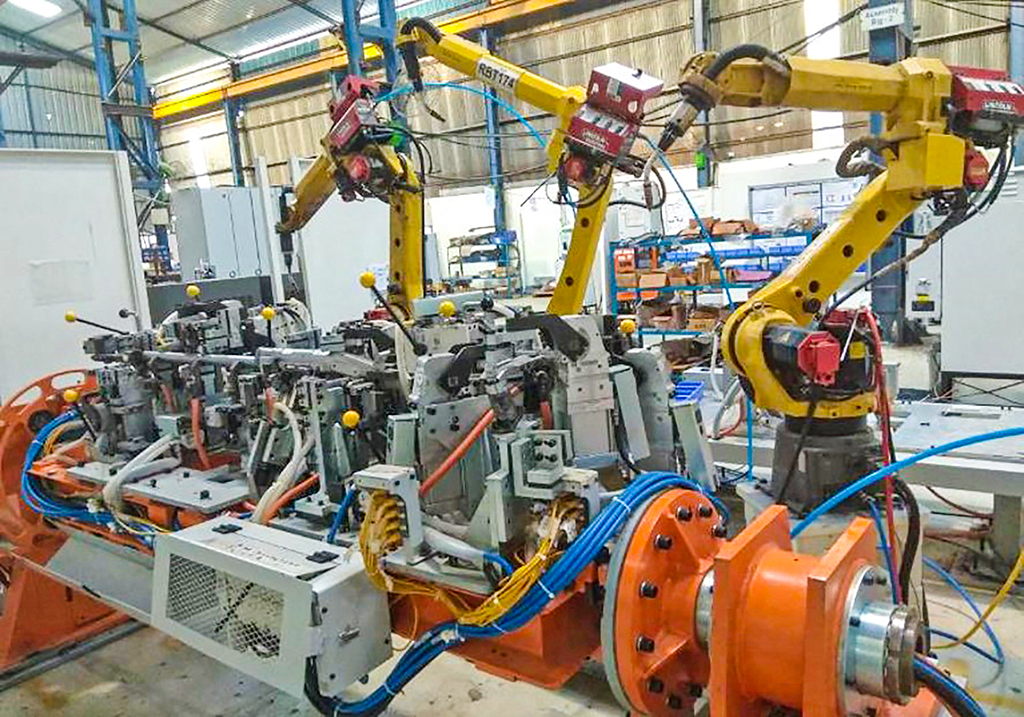
VDL Pinnacle is also eyeing smart lean factories that are being commissioned due to a lot of electric vehicle OEMs setting up shops in the country. Concludes Habbu: “A lot of these electric vehicle factories are looking at smart, green and lean manufacturing. They look at minimum layouts and enhanced productivity with minimum tooling and investment. This shall open a great business opportunity for us and we are happy to develop models for them. Given the order pipelines both with group companies (national and international) and the improving market sentiments, we are looking at 25% year-on-year growth and are excited about the prospects for the next 2-3 years.”