Tata AutoComp Systems, one of India’s leading automotive component conglomerates, has set up a division for electric mobility, spearheaded by Dr. A K Jindal, former head of research and development at Tata Motors. In an exclusive interaction, Rajesh Rajgor caught up with Dr. Jindal in his new role as an advisor for e-mobility, new products and technology to know more about the company’s plans for the future
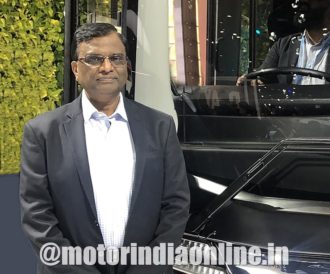
What is the company’s new EV division about and how will it drive the already established Tata AutoComp Systems?
When you talk about electric vehicles (EVs), there are 3-4 major components and systems. One is the battery, second is the driveline including motors and inverters, third is the thermal management and HVAC, and lastly, the miscellaneous power electronics. We have created partnerships over the last 12-18 months and have announced the same from time to time. One is a joint venture with Prestolite to design, engineer, manufacture and supply powertrain solutions for the Indian electric vehicle market. Prestolite is owned by the Broad Ocean Group of China and owns Shanghai E-Drive also.
The JVC will have access to technologies for various powertrain products like motors and controllers as well as integrated drivetrain i.e. integrated motor, inverter and transmission for all types of vehicles from two, three and four-wheelers as well as commercial vehicles. We have also established a JV with Gotion for battery pack and battery management systems. As you know, Tata Group companies like Tata Chemicals are working on cells, which will be leveraged by this JV. In addition, these existing business units are leveraging their in-house development experience as well as expertise from JV partners for thermal management and HVAC solutions for electric vehicles. Tata AutoComp has decided to go full-fledged into the automotive electrification sector. And as the market evolves we would be able to provide system solutions to most of the OEMs and lead the e-mobility transition in India.
TACO is also looking at power electronics as well as chargers so as to participate in the complete EV ecosystem. Beyond EV components, other group companies such as TACO Hendrickson have supported in development of air-suspension for 9-metre buses, a first-of-its-kind in the industry and mandated by customers, which has been integrated in 200 buses already commissioned in the field. Apart from only being system suppliers, Tata AutoComp wants to support the OEMs in architectural design and vehicle integration in terms of optimising the whole solution. In order to make EVs truly efficient, many components will have to be optimised. This new EV division will help us look for more holistic solutions.
As a company and as an industry, what according to you are the benchmarks to strive towards while developing an efficient EV?
On an operating cost basis, EVs are highly efficient as compared to equivalent ICE vehicles. While developing electric buses at Tata Motors, we have experienced that by following system approach as well as focus on detailed engineering for each and every component very high degree of optimisation in terms of cost as well as energy consumption can be achieved. Not only motors and inverters, every watt consumed by each and every major power-consuming accessory such as air compressors, hydraulic pumps and air-conditioning need to be looked at based on duty cycle and all possible losses, eliminated or minimised. Maximising regeneration while maintaining the vehicle dynamic and handling characteristics also helps in improving efficiency as well as improving the range. I can say that the kWh per km consumption levels that we could achieve would be quite equal or better than the benchmarks.
When you are researching, you may have to go through several permutations and combinations. How does a group like Tata AutoComp decide on standardisation that may fit for all vehicles irrespective of application or OEM?
You are right. There is always a trade-off between standardisation for the purpose of cost-effectiveness and better utilisation of resources and customisation to achieve the most optimum solution. In order to achieve best of both worlds, while designing the systems and aggregates, a platform approach is always thought of where you design the robust base and leave enough customisation possibilities to upscale and downscale to achieve the best fit solutions for a particular application. To give an example, for traction motors, whereas the base architecture of stator and rotor remains the same, there are many customisations possible through the modification of stator winding, magnet properties, length, etc. to achieve a wide variety of motor configurations.
When combined with invertors through suitable selection of ratings of some of the components, there arises the possibility of getting different torque, power and speed ratings to address the needs of various applications for a particular type of vehicle. To illustrate, a base drive line can be fine-turned for use in city bus application where the average speeds are quite less, and the same drive line when required for intra-city bus applications need tweaking for operating at high speed. Ultimately the objective of these tweaks is to achieve the best efficiency.
Given the nascent stage of EVs in India, what has been TACO’s contribution so far both in terms of standardisation and customisation?
As you rightly mentioned, the EVs in India are at a nascent stage and everybody is approaching the development based on what can be sourced as readily available systems and components from various suppliers worldwide. However, at TACO we are evaluating the requirements of driveline, batteries and power electronics for various vehicles being developed by various OEMs and developing reasonable standardised base designs which can be used for each application by some level of customisation. As an example, we now have a set of motor and inverter combinations with various torque ratings like 2,000 Nm, 2,500 Nm, 3,000 Nm and 3,300 Nm with can be used in all types of 9-metre and 12-metre buses with direct drive technology.
Similarly, we are gathering the requirements of all buses and developing modular battery packs which, by suitable combinations, can be used in 9-metre and 12-metre buses (standard floor and low floor) and give energy capacity of 200 kWh, 300 kWh and 400 kWh. We are also in the process of design and development of auxiliary drive, active battery cooling system and HVAC for all buses. Many of these can be easily integrated for trucks also as and when these are taken up for development. The next step shall be two and three-wheelers which are also quite amenable for standardisation and customisation trade-off. The same in cars can also be attempted, even though that may be a little more challenging.
Could you elaborate on the plans that will help Tata AutoComp’s transition from component supplier to a reliable system integrator in the e-mobility space?
At Tata AutoComp we are evaluating the EVs as whole rather than discrete systems. We are in a good position to achieve that as TACO has multiple businesses addressing various system requirements of a complete vehicle. As far as EVs are concerned, while offering solution to any OEM, we can evaluate the motors and inverters from our JV with Prestolite, batteries from our JV with Gotion, battery cooling system and HVAC system from AITTR, chargers and other power electronics and accessories in totality and offer the best optimised solution to meet the objective of optimum cost, range, weight and efficiency. Wherever the opportunity exists we can support the OEMs in optimisation of architecture of the vehicles in terms of integrating these systems. In fact, one of the key objectives of the EV team within TACO is to integrate various business units and drive efficiency.
In order to achieve the above mentioned objective, what we are planning is to have an engineering centre for hardware and software development and vehicle integration for all automotive applications. We are at an early stage of setting up the same and will take some time till we fully establish this entity. One way which will help us accelerate this is of course the global expertise from JV partners while another is through local expertise already available along with focused competence building. Definitely this value proposition will help us to work with all other vehicle OEMs just like how we work with Tata Motors. At the same time we are working within TACO with various BUs for developing a technology roadmap well-aligned with the growth strategy of TACO.
Just as we leapfrogged from BS IV to BS VI, how do you see the transition to electric vehicles?
It looks like every drivetrain will co-exist – be it electric, CNG, LNG, petrol or diesel. A lot of effort has gone into this leapfrogging, both in terms of technology adaptation and development as well as investment. Timing was very critical. Looking at the global experience with BS 6 equivalent standards, the emissions from new vehicles has become much cleaner. Anything better than that for ICE engines does not exist and standards are still under consideration. This is as far as standards are concerned. Even in the existing ICE vehicles more fuelling options such as LNG are likely to be available and explored. As you may know, Tata Motors has worked on LNG.
It may not be pan-India but has huge potential along the coastal areas where various LNG terminals have already been set up, as well as 500 km inland where LNG can be transported. This can do a lot of good in terms of energy security, environment and utilisation of available resources. If we have to clean up the environment, options other than only engine emission have to be explored. One of course is improving the transportation system, modes of transport, etc. Motivation for electrification is not only the emission but many other opportunities for improving the efficiency, energy security, etc. So, when looking at future cleaner technology it is evident that EVs will be the key enablers. In areas which are congested and polluted, electric vehicles will play significant role. I think, for quite a foreseeable future everything will co-exist.
While the potential is huge, in order to reduce carbon footprint, are we working towards getting the electric energy from a greener source?
Again, we have to take a holistic view. For transportation as well as electricity generation we are largely dependent on carbon fuels. There is no doubt that non-carbon-based power generation has to increase. The percentage of solar power-based energy is improving, but in my view, for a tropical country like India which is blessed with huge solar energy, we should leverage this to the maximum. The proportion of electricity generated from renewable sources is increasing fast. Hydroelectric is more or less static.
The biggest jump in green power has to come from the nuclear sector. So, we have to look at the total energy basket. Simultaneously, governments should also look at other measures to clean our cities. We have to make efforts to move away from individual transport to buses or public transport. Tata AutoComp is bullish and is focusing on developments in the EV space while looking forward to acquiring a much larger stake in electric vehicle system with most OEMs.