The third edition of the annual contest for mechanics – Technician’s National Skill Competition 2017 – organised by SML Isuzu at its Ropar truck plant on December 3 was well attended. Six finalists were screened from nearly 80 dealer teams that fought in the grand finale.
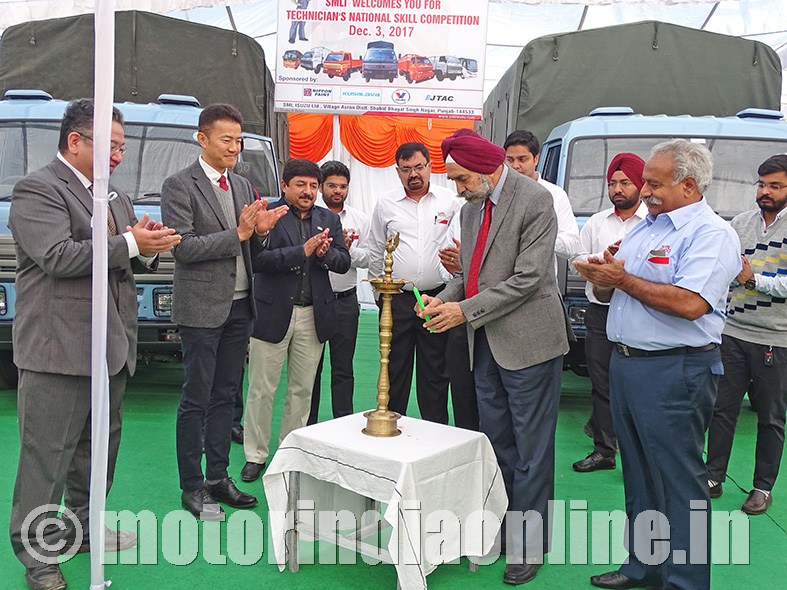
There’s no substitute for a technician’s skill in automotive service and vehicle management, more so for commercial vehicles in the Indian context. As engine technologies and complex electronics grow more difficult to navigate, dealer service centers and independent garages are realizing that they need access to more skill and not any less. This is in spite of the sophisticated service aids available these days and neat engineering associated with modern vehicles, which are supposed to make diagnosis and repairs hassle-free. Their customers are no more naïve and patient but are pretty serious in cutting the downtime of their fleet and demand superior quality repairs and service to their vehicles.
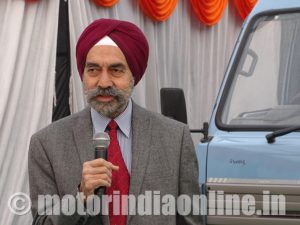
On the other hand, with stringent emission norms kicking-in, OEMs are increasingly realizing the heat of skilled-personnel shortage within their service networks at local levels. They understand the importance of local service delivery as key to market popularity and high volume sales. They are also certain that technical know-hows and skill training has to trickle down from their own resource pool to the lower levels.
SML Isuzu is proactive in imparting knowledge and skill training to their service technicians. The company has already operationalized two regional training centers at Bengaluru and Siliguri respectively, apart from the primary center at Chandigarh. These centers run professional training programmes for workshop mechanics on various technical processes involved in the service and maintenance of SMLI products. The company has strategically established these centers to have maximum coverage region wise, with local languages used as medium of instruction for better learning. To aid the training, the company’s technical team has introduced ‘Do it yourself’ videos and instruction compilation on various maintenance and repair processes to help the technicians.
From 2017, the company has also done away with the single module training course, and replaced it with three-levels of training – Level 1 (Beginner), Level 2 and Level 3. “Skill training forms the crux of service-level workforce
management at SML Isuzu, especially after the implementation of BS IV norms and the upcoming BS VI”, said Mr. Nawal Kumar Sharma, General Manager – Corporate Marketing and CRPM, SMLI. “Our target is to achieve 100 per cent L1 qualified workforce, along with 60 per cent L2 certified and 40-50 per cent L3 trained technicians by this year”.
Skill enrichment
Following the success of SMLI Technician’s National Skill Competition in the last two years, the third edition of the contest was even more vibrant with an increased number of participants from 75 authorized dealers. Each dealer team consisted of four members, including two technicians, works manager and a service engineer. A preliminary level of screening using a standard set of questionnaire was conducted earlier, and six top-ranked teams were shortlisted for the grand finale. There was a pan-India representation in the final pick, with teams hailing from Delhi, Faridabad, Goa, Vijayawada, Madurai and Tirunelveli.
Said Mr. Eiichi Seto, MD and CEO of the company: “This event is an active pursuit of the ‘ISUZU Skill Contest’ tradition that our Japanese partner periodically organizes. With changing engine technologies and service protocols, professional training for our technician workforce is stressed upon. This event is an effort to drive our dealers and technicians towards astute professional skills.”
He further affirmed: “We are sure that contestants will make an effort to wisely apply the professional knowledge learned from the contest to the enrichment of their service”.
At the final, the practical task for the teams was to solve a questionnaire by inspecting a given SML Isuzu T3500 BS IV truck. The teams were given 10-minute prep time and 45 minutes to solve the paper, along with service manuals and essential tool kit, including the ‘Digitech’ vehicle scanner and Vernier caliper. The participants inspected the truck’s engine health, lubricant levels, starting ability and electric utilities, and diagnosed errors. They were also assigned to check the outer diameter and the fillet radius of crank pin of a crankshaft and engine valves provided to them, to assert if they are fair enough to be used in an engine.
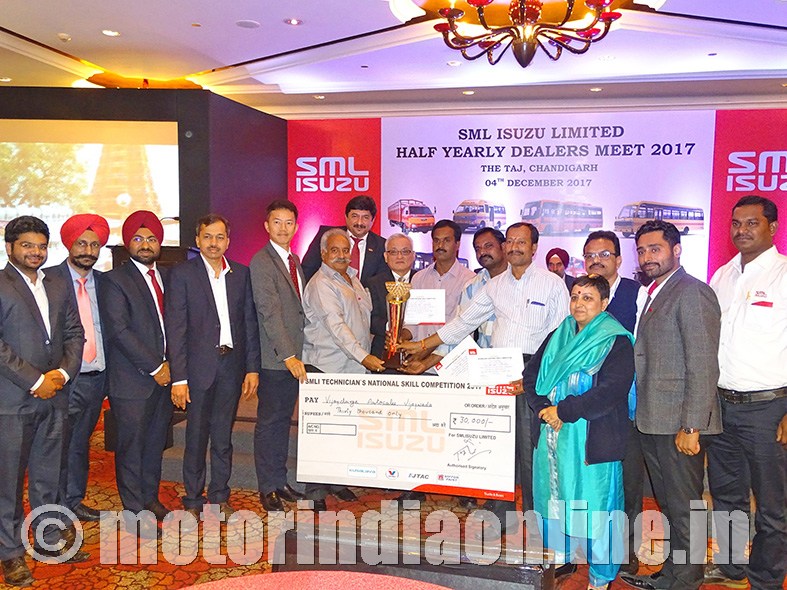
Each team was assigned two evaluators who kept an eye on everything that the participants were doing. They judged the team based on five parameters – safety and protection, inspection process, failure analysis, measurement and tool selection and usage. They also took note of the participants’ team spirit in supporting each other so as to finish the task on time.
The contest made the audience realize how steadfast and professional the SMLI technicians are to ingeniously and acutely get to the core of a misplay by the vehicle.
Team Vijaydurga Autosales from Vijayawada emerged winner in the final by scoring maximum points and took home a cash award of Rs. 30,000. HKS Automobiles of Faridabad and Rehoboth Motors of Tirunelveli settled for the second and third position respectively.
Asked about the expansion of the skill contest, Mr. Sharma said that the next edition will consist of similar practical tests at the three regional training hubs to screen the participants for the final round.
“Dealers’ response to the event is great, and the number of participants is increasing year after year. We are also trying to bring the technicians of independent garages dealing with SMLI products into our training grid and skill contest so as to promote certain best-management practices like using genuine spares”, he added.