Prakash Seating Pvt. Ltd. (PSPL) has turned a new leaf over in a mere 10 months since we last visited their factory premises. This young company had at that time revealed a series of initiatives and business growth strategies to create a strong identity for itself in bus passenger seating segment.
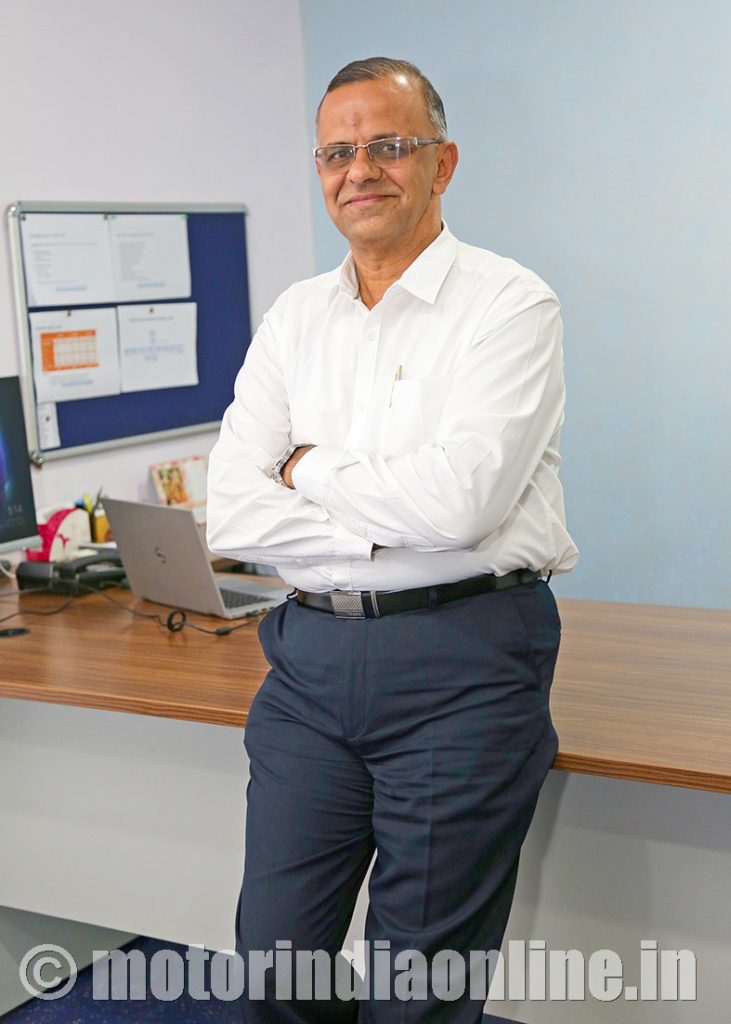
In our latest interaction with Mr. Rengarajan Srinivasan, Director, and Mr. Pradeep Ambavaram, Director, it was apparent that most of the goals that they had set for themselves last year have either been achieved or just on the brink of fulfillment.
While continuing to ensure ‘customer delight’, the duo is working towards exponential growth in the current year as against 45 per cent growth achieved last year. As the motto stood at “exceeding customer expectations”, there is visible improvement on the quality be it products, services and people in the business environment. Continuous improvements across the business processes enabled to deliver efficiently.
Prakash Seating as a team, under the energetic leadership of Mr. Rengarajan Srinivasan, has worked towards achieving total quality management. It has implemented quality management system (QMS) with TS-16949 in place. The products serviced to customers are compliant to test certification requirements for the seating business.
Mr. Rengarajan shared: “For achieving the key business objectives with higher production and sales targets, we have already doubled our capacity and plan to add another 100 per cent by the year end. This will enable PSPL to achieve over 100 per cent growth in turnover.”
Mr. Pradeep said: “We continue to work towards achieving ‘stakeholder delight’. With collaborative support from our supplier partners, we are on our way to achieve most of the goals we had set for ourselves.”
PSPL currently holds a capacity close to 6,000 bus sets a year on a single shift production, while second shift option is also pursued. This includes both reclining and fixed seats, berth foams and seats for city buses.
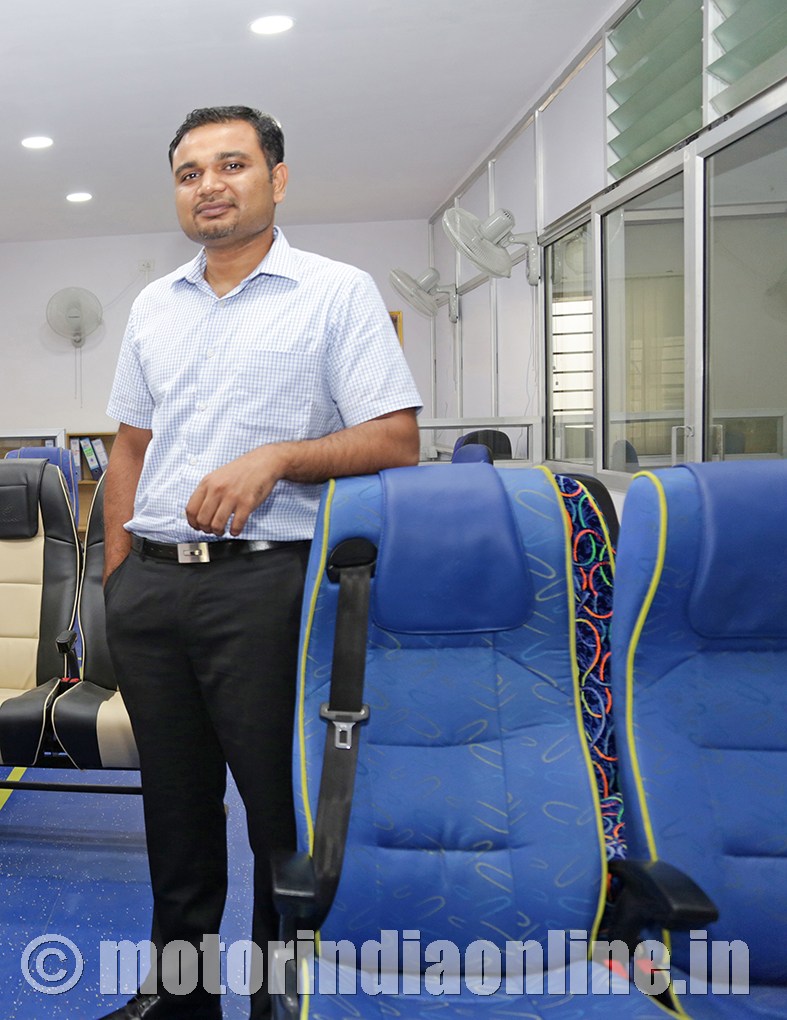
With a slew of automation in place now, PSPL is manufacturing seats with increased productivity and reduced cost of manufacturing. In fact, automation on the shop floor has sped up deliveries. It has helped them raise the bar on number of bus sets of seats and foams delivered per shift, using fewer number of workmen and in reduced space.
Mr. Rengarajan added: “Our make in India designs are innovative, and we are successful in achieving our material and manufacturing cost targets. We have range of our own products to cater different bus industry segments like inter-city coaches, district Mofussil buses and urban city buses. Our berth foams are manufactured using our own design and the foam itself is becoming a product to the body builders for the sleeper coaches. The next step is to offer modular sleeper berth to the body builders.”
Integration, efficiency and productivity
Mr. Rengarajan said: “As we build capacity and deliveries, the investments on resources may not be proportionate and is tightly controlled per necessity. Otherwise it is getting offset by automation, efficiency and productivity improvement. For the press parts, tubes and components, we demand the suppliers to deliver material as per our daily shift requirement and with control over quality. As a result, suppliers deliver on time in full and we do not need to store more than what is required. Besides manufacturing the foam and seat assembly in-house, we have brought welding and upholstery processes in-house, which are leading to expedited deliveries. Today, we have the capacity to be flexible in product mix and scalable too, improving efficiencies and productivity.”
According to him, the initiatives that were implemented in the last one year including firming up of policies, quality improvements across products and processes, data management and management information system (MIS) for business metrics are bearing fruits now.
There is greater focus on significant reduction in the PPM measure across supplier parts, in-house processes and delivered products. This is achieved through continuous improvements on part to print compliance, improving endurance test requirements of critical parts influencing the performance of seat mechanisms and building reliability engineering concepts from design to manufacturing.
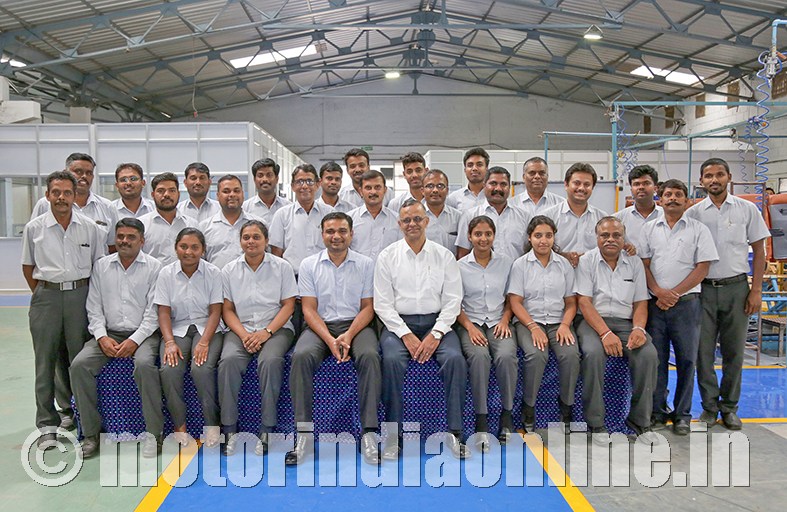
PSPL aligned its focus on cost reduction initiatives by introducing innovations in productivity and processes, so that profit improvement can be realized. Another crucial activity that PSPL has embarked on is mapping the employee skills and is now offering training to its employees.
PSPL is objectively focusing on top-line sales, cost reduction initiatives, profitability, quality and customer satisfaction. “PSPL is pursuing organic growth from existing products by expanding the customer base, market penetration and higher share of fitment at body builders. With strategic pricing and marketing, we plan to obtain STU tender businesses and fully built bus seats. Our focus is on bringing innovative products on modular platform, with light weight and futuristic customer expectations. Further business growth will come through new products being launched, new customer acquisitions, new territories and OEMs. Future growth strategy of PSPL includes new products in the current businesses, exports and new line of components”, concluded Mr. Rengarajan.