Designer and manufacturer of specialised lifting and handling solutions, Nandan GSE is aiding clients improve operational cost, productivity and safety. Rajesh Rajgor shares the details
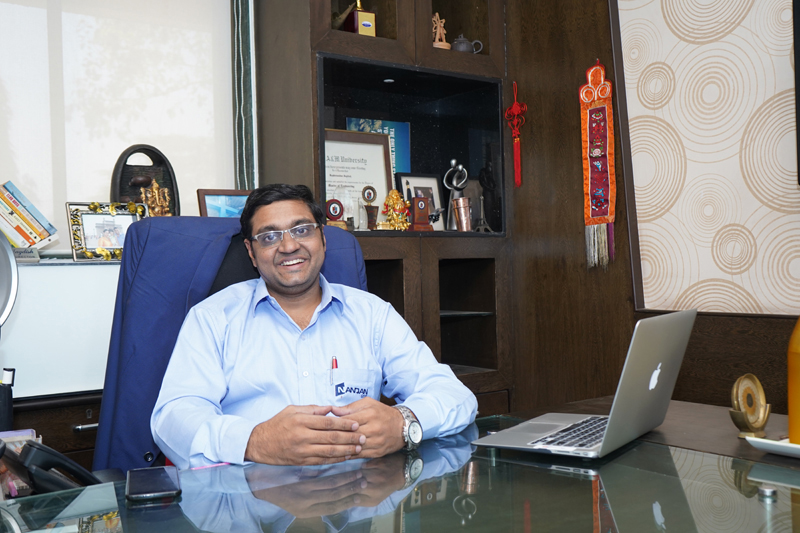
Established in 1991, Nandan GSE has been recognised for many years now as one of the finest companies to have emerged from the Indian innovative aviation ground support equipment (GSE) manufacturing and hydraulic lifting systems. With applications in the aerospace, aviation, defence, material handling, aerial access equipment, car parking and similar sectors, the company has carved a niche for itself in providing lifting solutions that effortlessly boost operational efficiency. The result is improvement in client’s productivity, safety and operational cost.
The company achieved quite a feat recently when it delivered a high-loader (hi-lift), passenger stairs and other GSE equipment that makes ground handling operations easy and safe for airlines across the world. The company has made great progress in coming up with a new small high-loader of the BS IV-compliant version on the Bharat Benz chassis. This vehicle design leads to a 70% increase in capacity over traditional high-loaders with no increase in overall dimensions on the road. With customers increasingly requiring small high-loaders for servicing small aircrafts with long-haul catering service support, Nandan GSE set about optimising efficiency throughout the long-haul supply chain.
A key objective was to increase the capacity of the traditional high-loader while complying with global operating standards and maximising fuel efficiency while in operation. “We also stretch every nerve to improve acoustics comfort by minimising irritating noises. That’s quite a challenging task which takes years and years to perfect. Fortunately, we understand that a good chassis is the starting point for good acoustics. From there you can solve smaller issues over the years. The new design is predicted to cut operating costs by around 20% for the client,” informs Raghunandan Jagadish, Managing Director and CEO, Nandan GSE.
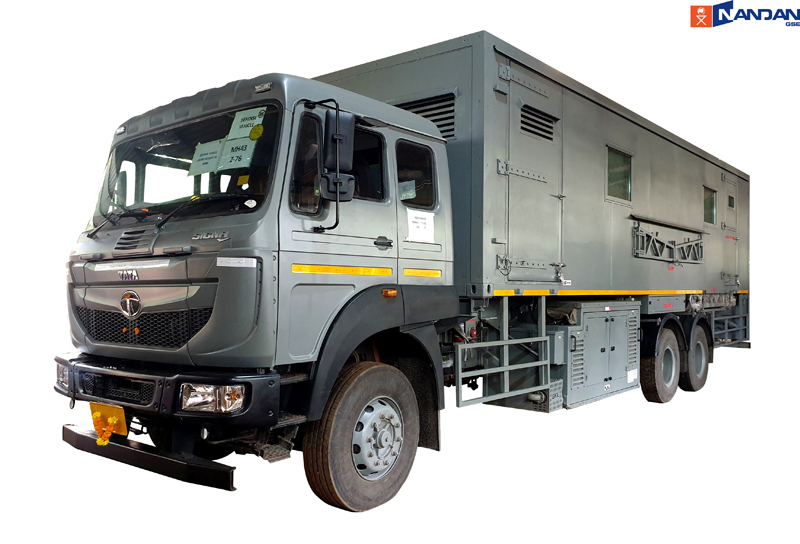
Value for Money
Founded by J C Kumar, Nandan GSE is a 30-year “young” company that employs over 150 people today. It meticulously works on its founder’s vision to make the world of specialised lifting and handling a safe and profitable space. When asked about bridging the gap between a cost-effective product and an efficient product, Jagadish says, “I have a very firm belief that the price is what you pay and value is what you get. If you buy something for cheap, it shall give you problems in the long term. We educate customers and tell them that if you invest in capital expansion, your operational expenses go down dramatically.”
“Once your quality is up your downtime is marginal as the amount spent on spare parts, service and accidents is mitigated. Hence, we talk to customers, understand what is it that they want to address and offer them the optimum solution. Our customer realises that by paying 40% more compared to the garage products, the life of the vehicle will be utilised for 10 years without any issues. Further, it would avoid accidents, threats to human life and help in completing the project faster. Our equipment leads to higher uptime owing to its lubricant-free system. You don’t need to grease or change the pin as it will last for the life of the equipment compared to someone who puts gun metal and does not grease for a month,” he adds.
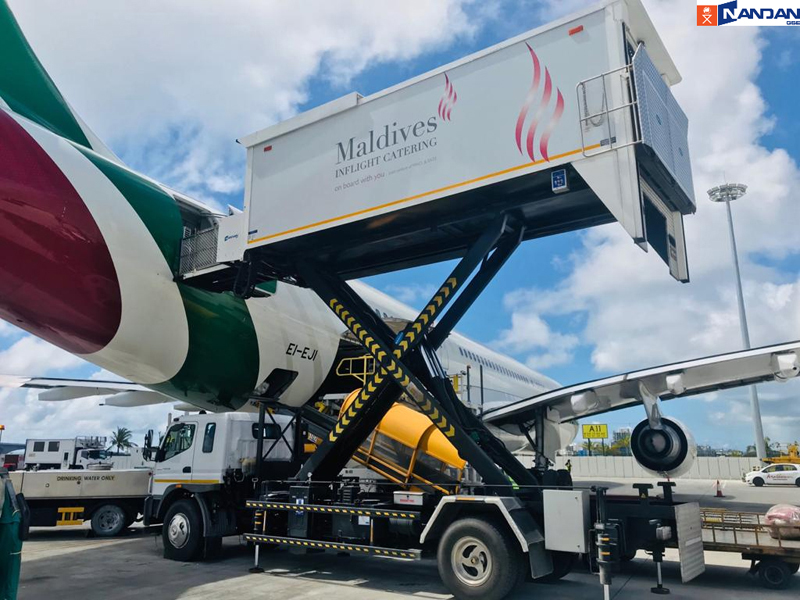
Concerted Efforts
It is evident that Nandan GSE places prime focus on customisation which cannot be achieved without firm processes, training and optimisation. In other words, the emphasis is on quality checks, skilling and offering value for money. Says Jagadish: “The customer’s profile is maintained in our ERP right from buying the material to its traceability and until the last cut is measured. Our quality checks ensure that the dimension, chemical composition and material are correct. Almost 10% of the material is always kept for quality checks (QC). We have a 200-point check list which the QC has to run through before it is signed and considered fit for delivery. Our stringent process ensures that customers trust us and hence most of them don’t even test the final product. They have complete faith in our methodology.”
Operating out of two factories with over 65,000 sq. feet of production shop floor space in Turbhe and Khopoli in Navi Mumbai, Nandan GSE’s processes are driven through a custom ERP. Elaborates Jagadish: “Right from the pre-sale to getting a sales order and delivering the project to the customers, everything is aligned on ERP. Our customers are also integrated on it so that they know where the project is headed. We have a very strong process ownership starting from marketing owner, job owner, planning owner, design owner, QC owner and a complete project owner. These five people form a cell for a project. Additionally, we do bespoke model for clients and don’t really have an assembly line. Apart from welding, bending and painting we outsource the work to vendors that meet our quality standards.”
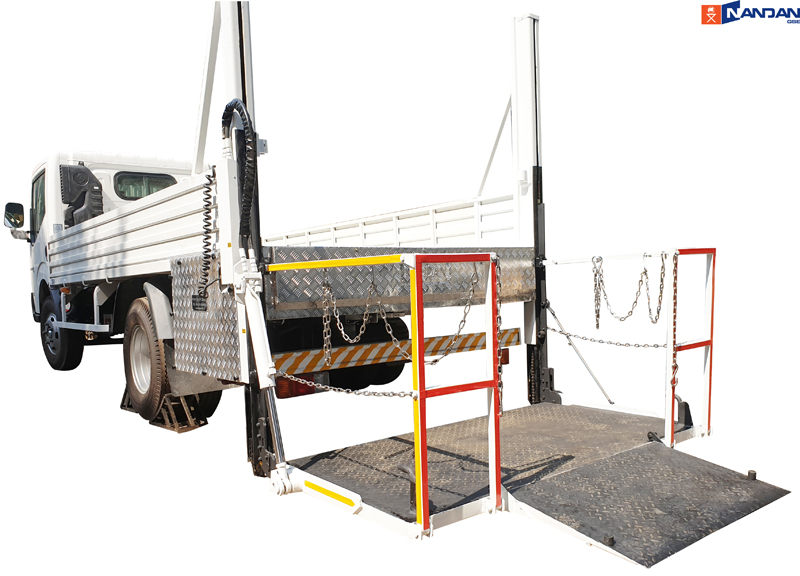
Customisation and Innovation
When it comes to product offerings, Nandnan GSE has been quite successful in the aerospace and defence sectors thus far. The company has delivered products like vehicle-mounted scissor lifts, special purpose catering lifts, hydraulic tail lifts and portable truck loading platform, among others. Just before the pandemic-triggered lockdown, the aerospace industry was moving towards electrification and Nandan GSE has been attuned to this trend. “Regulatory authorities are working on implementing improved guidelines towards the development of eco-friendly processes and technologies. In the long run, most of the diesel-powered vehicles will transition into electric ones and so we have worked on creating a prime mover with battery packs and IOT devices,” Jagadish informs.
“We have made lifters, truck-mounted crane and knuckle boom crane from 2-50 tonne metres, among others. We are also working on self-propelled 100 tonne scissor lift. This loaded tipper truck will climb on to the scissor lift and tip into the wagon directly,” he adds. In the same breath, the ‘catering champ high-loader’ is the latest in a series of innovations that the company has introduced in recent years as part of their ‘Go Green’ initiative. “We are committed to delivering significant environmental improvements for our customers. The initial response from our customers suggests that the new catering champ high-loader is set to have an equally dramatic impact,” he says.
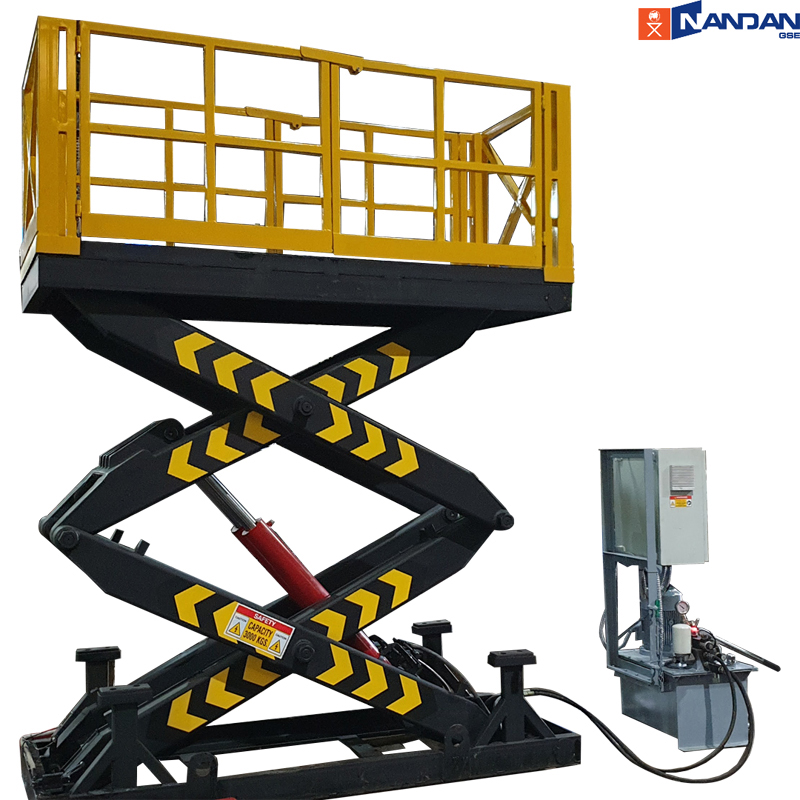
Nandan GSE is also focusing on weight reduction for various applications like container tilters, pool dollies, knuckle boom cranes, tail lifts, etc. “The demand for container tilters is rising and we have addressed the challenge of entirely lifting the container, especially in the sugar and mineral industry. This will be a revolutionary system for the industry. The same goes with tail lifts, truck loading or unloading platforms and zero scissor lifts. When it comes to offering value, we are making lighter bodies and working with FRP, sandwich panels and carbon composite materials to offer weight reduction,” informs Jagadish. Reiterating the company’s mission of ‘value selling’, Jagadish explains how the team at Nandan GSE customises solutions for its clients. For instance, a logistics and freight forwarder contacted Nandan GSE for an optimum solution for their truck loading issues which caused unsafe loading and unloading of pallets from the truck bed to the ground level.
Moreover, the major issue was that they could not afford to block their warehouse entrance with a conventional set-up for the problem. “After evaluating the situation and understanding the client’s needs, we advised a zero scissor lift. This serves the purpose of loading and unloading of goods from the truck bed level to the ground level for the pallets while also keeping the warehouse entrance free as the zero scissor lift is flushed to the ground when not in use,” Jagadish explains. The client benefited tremendously as the safety level increased on account of reducing manual labour. The results also increased productivity on account of reduction in time taken for loading and unloading and provided flexibility of moving the zero scissor lift due to the provision of wheels.