A leading solution provider to all sheet metal and tubular frame fabrication needs of global automotive OEMs in the country, the company claims to leverage its first-mover advantage of embracing precision automation and Industry 4.0 in becoming ‘one-stop shop’ for all fabrication needs of automakers. In conversation with Mr. Nishant Jairath, Director – Metalman Auto (P) Ltd.
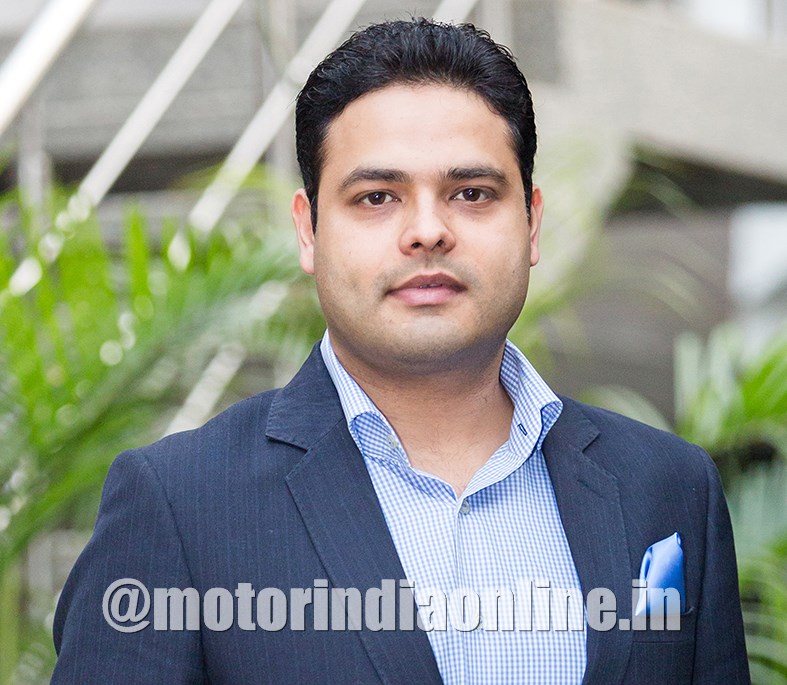
The metal frame assembly is perhaps the most critical component in a motor vehicle, as it gives the essential structure to the machine – just like a human skeleton made of multiple bone arrangements that gives our body shape, support, flexibility and movement – upon which all other aggregates are attached. The sub-assemblies are likely to be the first chunk of auto parts that are put on the assembly line at the automakers’, something that are typically cherry-picked by vehicle makers from the best of design and quality that they can find among their suppliers.
And for a component supplier specialised in manufacturing those metal frames, things are not that easy either. These are custom-made products with a plethora of designs and variants to suit every single vehicle model, while their criticality factor calls for the fabricator to be present close to the OEM and perform just-in-time delivery, as volumes are huge, especially in case of motorcycles and three-wheelers. The supplier has to have an enormous capability base – technological and resource power – to cater to such demanding needs of their OEM clients, while also practicing frugal manufacturing to remain cost-competitive in the industry.
But to Metalman Auto, a manufacturing house that rolls out 12,000 motorcycle frames on a daily basis, the aforementioned heat is nothing but a piece of cake! A premier manufacturer of sheet metal and tubular fabricated assemblies and sub-assemblies predominantly to two-wheelers, three-wheelers, and off-road vehicles and construction equipment, the company is aggressively expanding its product portfolio and client base, with a slew of dedicated greenfield facilities for select clients and superior levels of automation.
“With an experience of over three decades, we are widely recognised for supplying customised and defect-free parts at a competitive price and at right time to a wide range of automakers and export clients. This is possible because of our concerted focus on automation and resource management”, says its Director, Mr. Nishant Jairath.
The company’s product portfolio includes sheet metal aggregates like driver cabin (for three-wheelers and off-road equipment), air dust covers, oil pans, chain case, engine guards, etc., and tubular products like steel frame and carrier frame assemblies for motorcycles, exhaust mufflers, handle stem and bars, crash guards, and so on.
Quantum leap in automation
Tracing roots back to its paternal company National Industries based in Ludhiana that today produces headrest rods for cars and nickel-plated motorcycle handlebars, Metalman Auto ventured into fabrication of motorcycle frames for Kinetic Honda in 1986 with a plant at Indore. But the company was incessantly groomed by Bajaj Auto starting from 1996 onwards as a strategic partner. Even today, the OEM is the prime time client in terms of volume, with a dedicated state-of-the-art manufacturing facility at Aurangabad. A joint venture plant under Metalman Micro Turners at Rudhrapur is also catering to the fabrication and surface treatment of products meant for Bajaj Auto.
The next break for the company came in recent years in the form of new OEM engagements and export opportunities. Metalman Auto has established three greenfield projects dedicated for Hero MotoCorp, TVS Motor and Royal Enfield at Dharuhera, Hosur, and Chennai respectively. The Chennai plant will become operational in a couple months while the other two are already active. Further, the company has dedicated one of its plants for export to global brands like Harley Davidson and BMW Motorrad alike.
While revealing that the Rs. 750-crore worth Metalman Auto and the Rs. 400-crore worth Metalman Micro Turners are registering a year-on-year growth of 40-50 per cent in recent times, Mr. Jairath acknowledges the phenomenal role of automation and precision technology their exemplary growth. “We have first mover advantage in terms of adopting automation, as we invested on cutting-edge robotics and other lean manufacturing technologies some 7-8 years back, much ahead of the industry. Today, most of our competition are just embarking on basic automation, while we have moved ahead to the next level of incorporating Industry 4.0 in our manufacturing”.
He adds that the benefits of machine learning, wherein robots can become flexible enough to learn and correct themselves, are immense in metal fabrication and that his company is working with different tech partners to take automation in their facilities to a whole new level.
He also maintains that automated manufacturing is frugal, thus giving a competitive advantage to his products. “Automation offers different ways to capture maximum ROI by employing numerous sensors and precision technologies, making the entire process more effective and efficient in every aspect possible”. Automation using robotics is very effective for product lines that have a lot of variants, as high-tech robots employed by Metalman Auto support multiple fixtures and functionalities. This helps in diversifying our product portfolio and business viability, he added.
Off-road and commercial vehicles
In terms of product design and related R&D, the Director opines that OEMs adopt ‘Design for Manufacturing’ principles wherein they involve component suppliers in designing and developing print for products they require. “There exists new synergies of research and development from both our side and that of the automaker. We understand their fine requirements and deliver what they want”, he says.
Asked on the emerging megatrends of electrification, he replies that his business is largely protected from on-going disruptions, but there are new opportunities and learnings one should tap on.
He revealed that Metalman Auto is already working with few global tech-based automotive firms on the lines of developing effective vehicular frames for EVs and steel enclosures for their battery packs.
In terms of business prospects in future, the company is anticipating a good growth in products for off-road and CV applications. Metalman Auto is involved in complete fabrication of driver cabins for tractors and construction equipment, including that of metal frames, glass pasting, painting, and assembly of interior trims sourced from vendors. OEMs like Escorts, Sonalika International and CNH Industrial have partnered with the company in this regard.
“We are currently betting big on this business vertical, which also has an ample export opportunity. We have recently signed an MoU with a Canadian firm for a buy back arrangement, which may evolve in the next two years into a JV, with a manufacturing facility set up in the US to cater to North American markets”, Mr. Nishant Jairath noted.
Further, the company has also embarked on manufacturing sheet metal products for commercial vehicles, like oil pans, foor steps, linkages, brake pedals, and so on. It is now supplying products to Ashok Leyland and Mahindra Trucks and Buses, and the Director is determined to crack this segment as well.
The Metalman Group grew almost 100 per cent in the last financial year, Mr. Jairath claims, while adding that the target is to surpass the Rs. 1,500-crore mark by 2020 and Rs. 2,000-crore by 2022-23. “Our focus right now is entirely on building a human capital and resource base to support such high growth numbers. We sell not just products, but our capabilities. So, preparing ourselves to the demands of our clients and the market is crucial”, he observed.
“We have first mover advantage in terms of adopting automation, as we invested on cutting-edge robotics and other lean manufacturing technologies some 7-8 years back, much ahead of the industry. Today, most of our competition are just embarking on basic automation, while we have moved ahead to the next level of incorporating Industry 4.0.
– Mr. Nishant Jairath, Director, Metalman Auto