Understanding the pulse of the Indian customers, drivers and operating conditions, the home-grown company has come up with an ‘Indian product for Indian roads at Indian price’, reports N. Balasubramanian
Jamna Auto Industries Ltd. (JAI) has been engaged in the leaf springs business for more than six decades. JAI is the world’s third-largest spring manufacturer with eight manufacturing facilities spread across different parts of India. While leaf springs are used in mechanical suspensions, JAI began developing air suspensions with lift axles in 2011 for the Indian market in collaboration with Ridewell Corporation, USA. This lift axle air suspension was very well-accepted by the Indian automotive industry and a majority of OEMs started using JAI’s lift axle air suspension within 2-3 years of its introduction in the Indian market on rigid trucks.
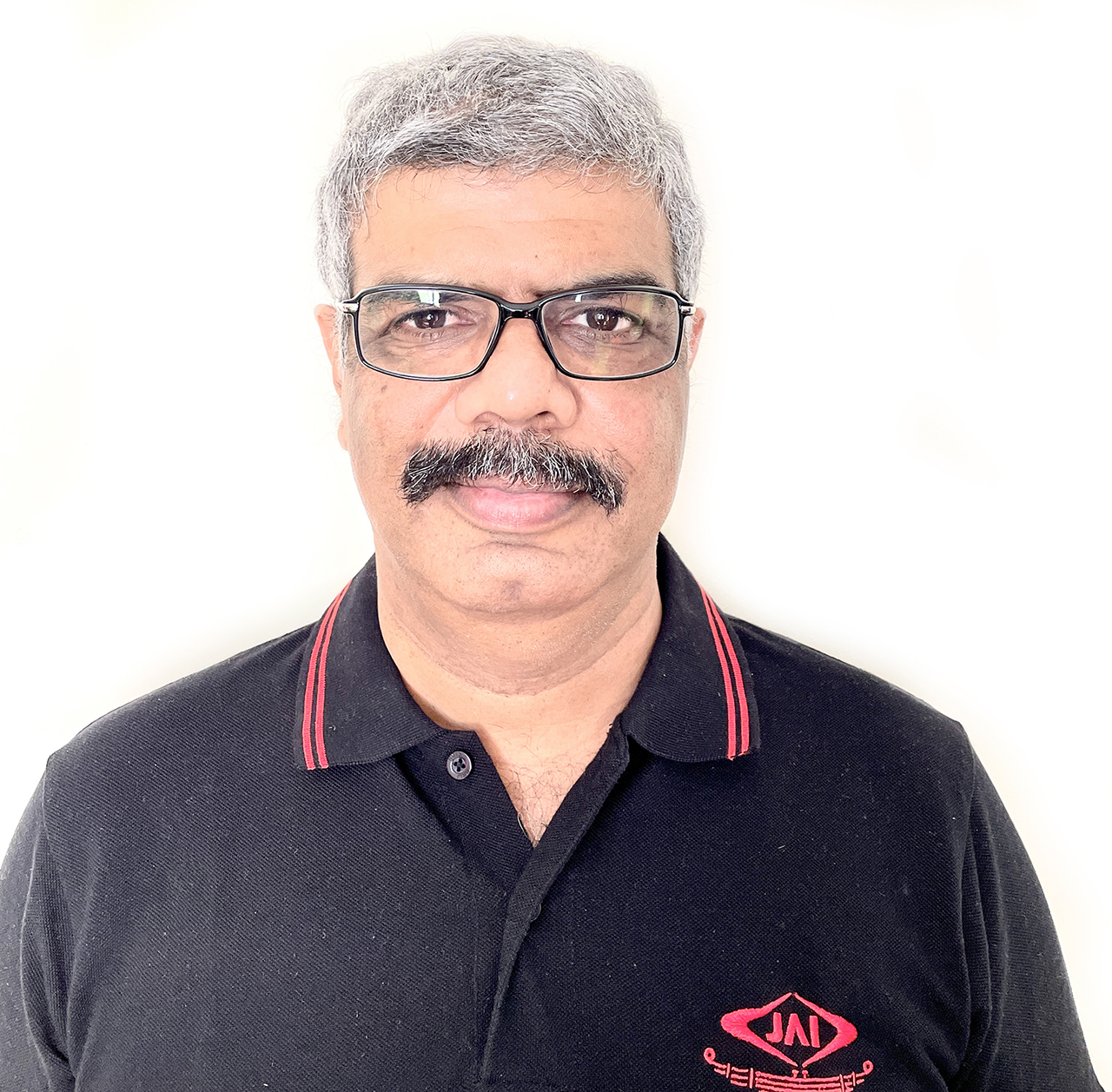
Seven years later, JAI identified another major opportunity in the market. “As soon as the new axle load norms came into effect in July 2018, wherein it was allowed to carry one tonne of additional load per axle if fitted with air suspension, we pressed our aftermarket network into service to collect data from major trailer fleet operators. We also used this opportunity to educate them on the advantages and features of air suspension,” says Sunil Laroiya, President, Jamna Auto Industries. While the field study was underway, the company’s research and development team at Pune started design and development work on air suspension system for trailers in order to ensure that it could introduce the most appropriate product for Indian road conditions in the minimum time possible.
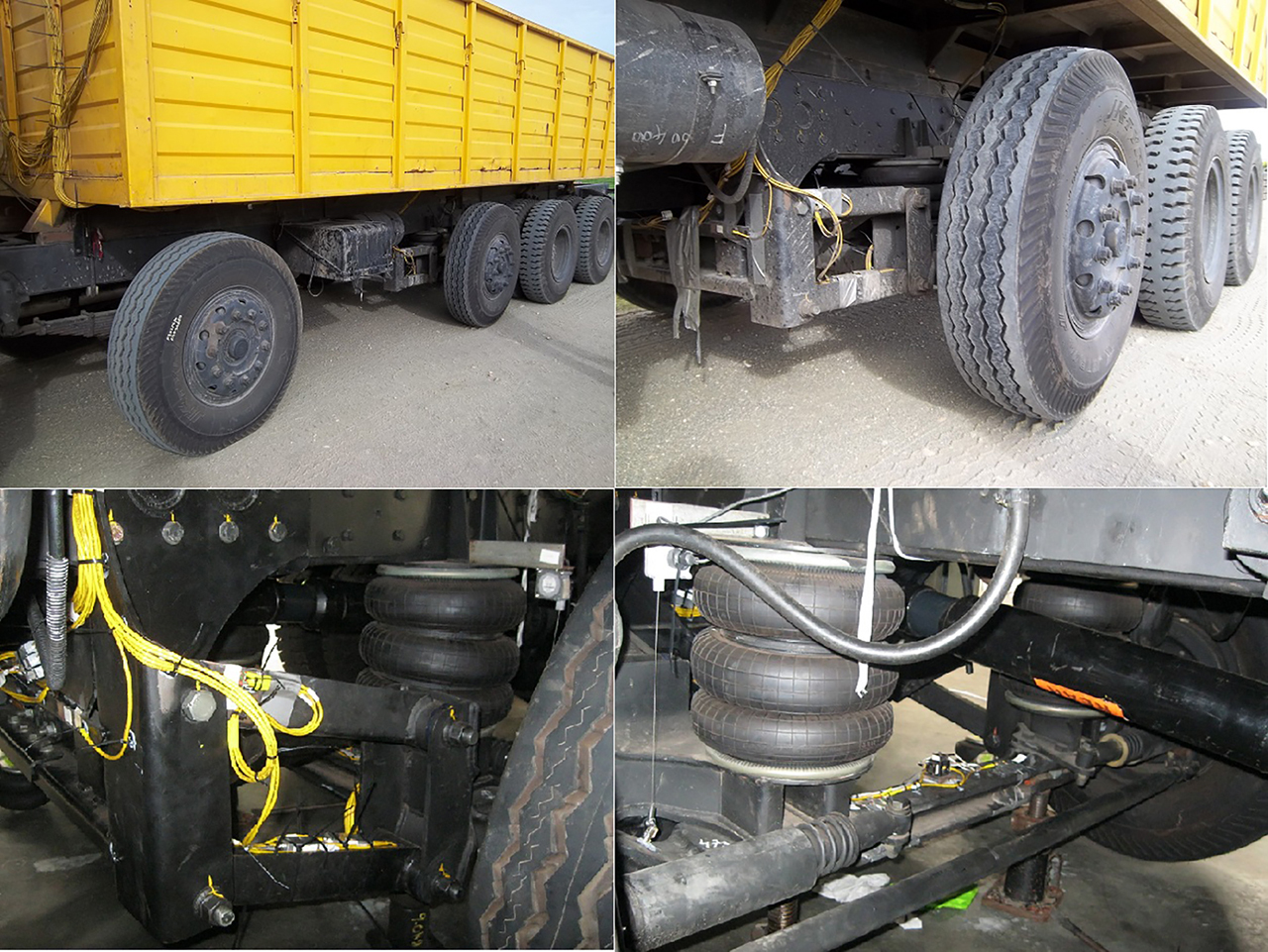
“Our team worked tirelessly and developed initial prototypes within six months’ time. Their rich experience in working on rigid trucks’ lift axle air suspension system played a huge role in bringing the best-in-class air suspension for trailers in the minimum time possible,” Laroiya states. While JAI has state-of-art research and development and test centres equipped with six servo actuators to test any kind of component or complete suspension system, the company decided to test one suspension at the Automotive Research Association of India (ARAI) in order to ensure the reliability of the product.

“After successful testing at ARAI, we performed some more tests at our in-house test facility to ensure the reliability of the product. After initial ARAI and in-house testing, we fitted our indigenously designed and developed air suspension on a few vehicles in order to get field feedback. These initial fitments gave us extremely valuable inputs which are generally not captured during laboratory rig testing. We further strengthened our product based on this initial field feedback and it was ensured that the complete structure and all crucial components like air bellows, dampers, bushes, etc. would withstand the harsh Indian road conditions,” Laroiya adds.
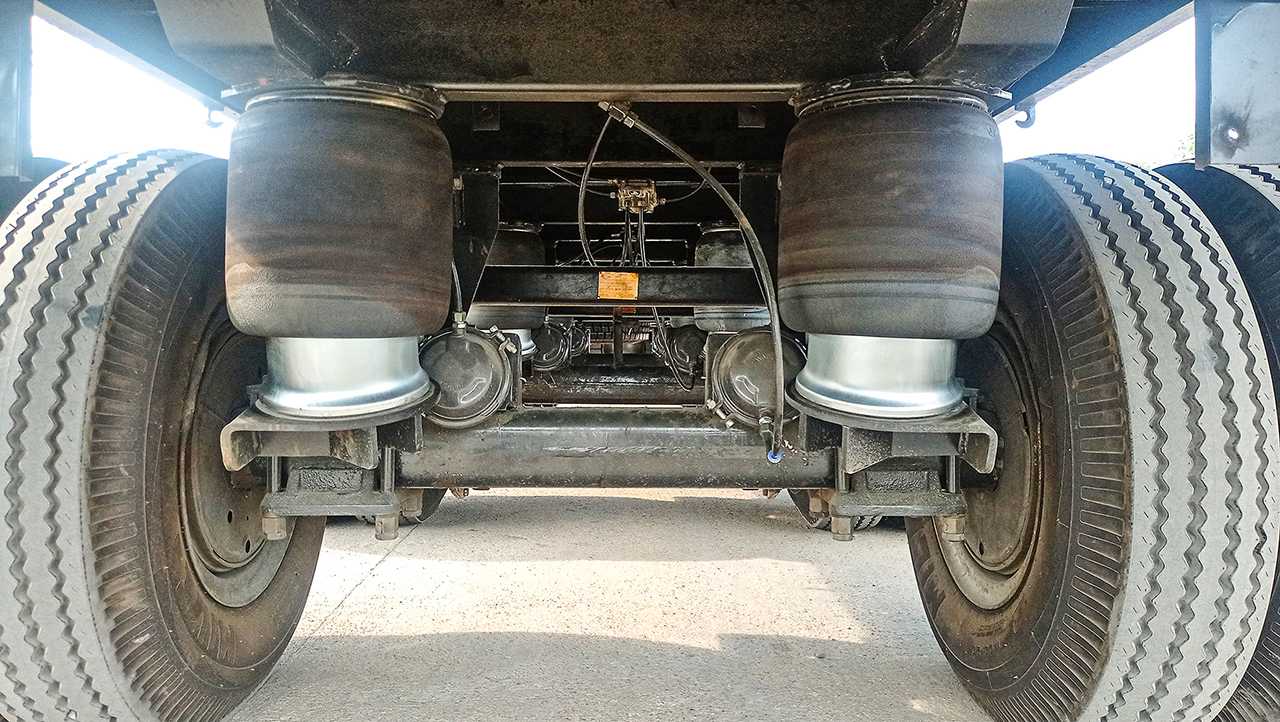
The engineers specifically designed air bellows for this particular application instead of picking a product from the standard catalogue. Most manufacturers pick up bellows from the catalogue and fit them on the suspension, which does not give expected results in Indian conditions. “Our team extensively studied not only the design but also the manufacturing process. These bellows have gone through extensive testing at ARAI and at our internal lab to ensure that the product qualifies to match the needs of the harsh Indian road conditions,” Laroiya reiterates.
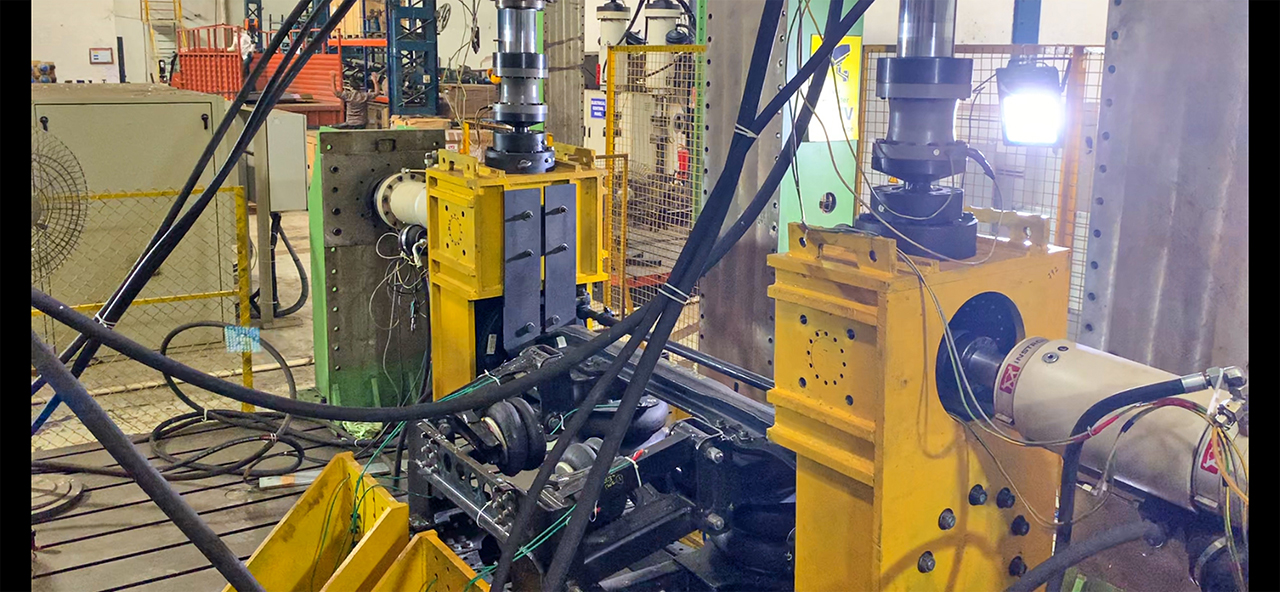
While developing trailer air suspension the company also introduced lift axle similar to rigid trucks so that one or two axles out of three can be lifted whenever the trailer is running in a non-laden condition. This ensures that operators can save on tyres while the trailer is running without or less load. The lift axle module can also be retrofitted on old trailers in combination with mechanical suspension. Operators can use the existing mechanical suspension on two axles and can replace the third axle with lift axle air suspension so that this particular axle can be lifted whenever the trailer is running empty or with less load.
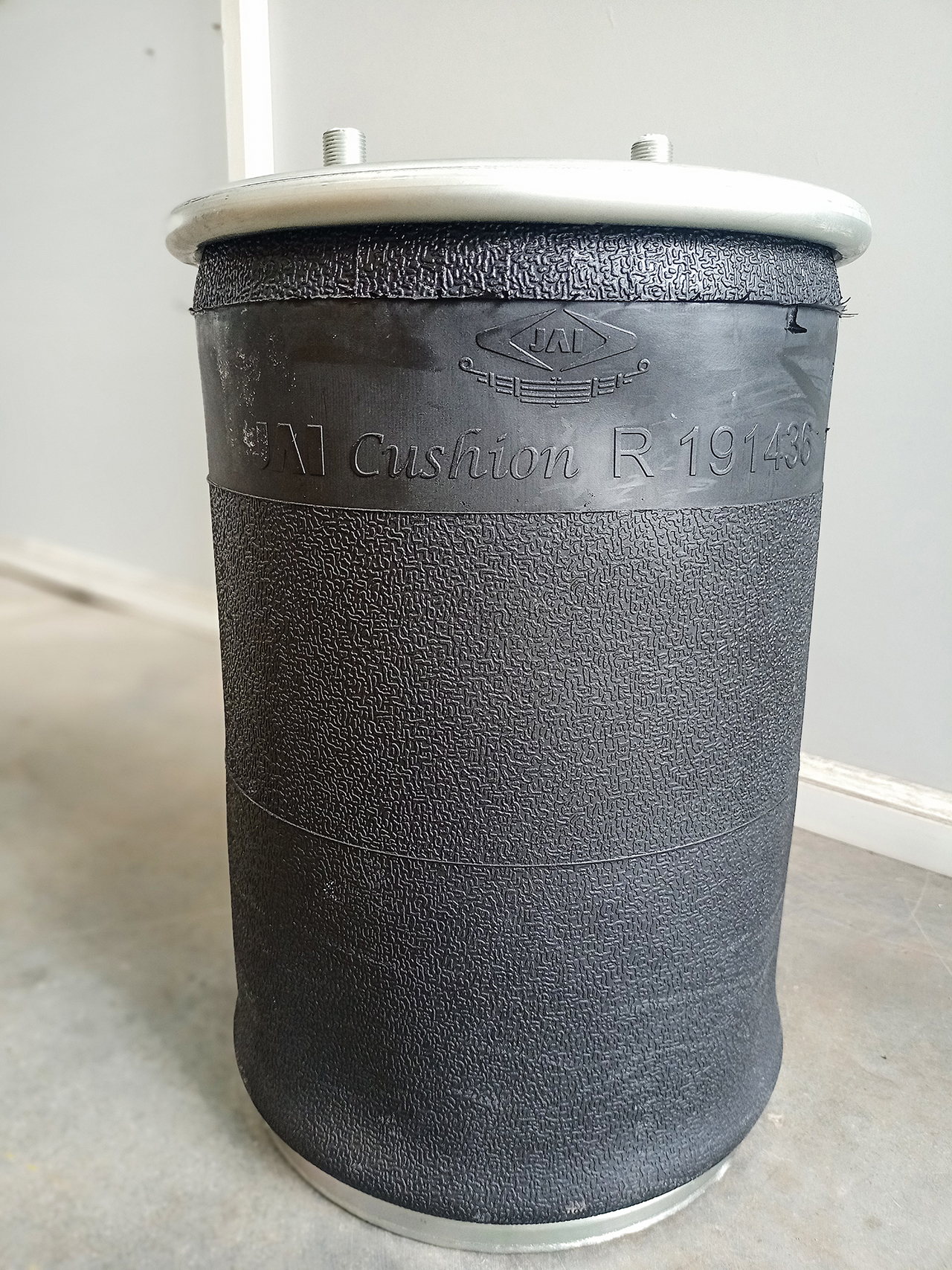
This kind of combination was successfully introduced by JAI in rigid trucks for OEMs more than a decade ago and created a huge demand in the market in rigid trucks. JAI expects similar kind of demand in trailer suspension also. “JAI has a major advantage over other global brands entering India since its suspension has been designed for Indian road conditions from scratch instead of introducing an off-the-shelf product. It is extremely important to understand the pulse of the Indian customers, drivers and operating conditions before introducing a new product in India. The Indian market needs reliable, maintenance-free products at competitive prices. This is what JAI has introduced – an Indian product for Indian roads at Indian price,” Laroiya states.
The other major advantage JAI has is in the form of its research and development centre situated in Pune where it can test the smallest component to a complete suspension system. The team at this centre is continuously engaged in generating data not only for the complete suspension system but for each critical component that goes into the suspension system. “We keep testing parts under different load conditions in order to simulate the real world conditions. This database helps us a lot whenever we introduce a new product in the market. Currently, our lab is operating in all three shifts in order to meet the workload of many more products that JAI plans to introduce,” Laroiya informs.