The more the complexity of a problem, the happier they are – Igus India works in different domains and automotive sector holds a keen interest for the company. Sarada Vishnubhatla catches up with Deepak Paul, Managing Director and Santhosh Jacob, Country Manager and Director at Igus India, and gets them to talk in detail about how the company is slowly yet steadily making space for their products in vehicles which have mostly metal products for their innards.
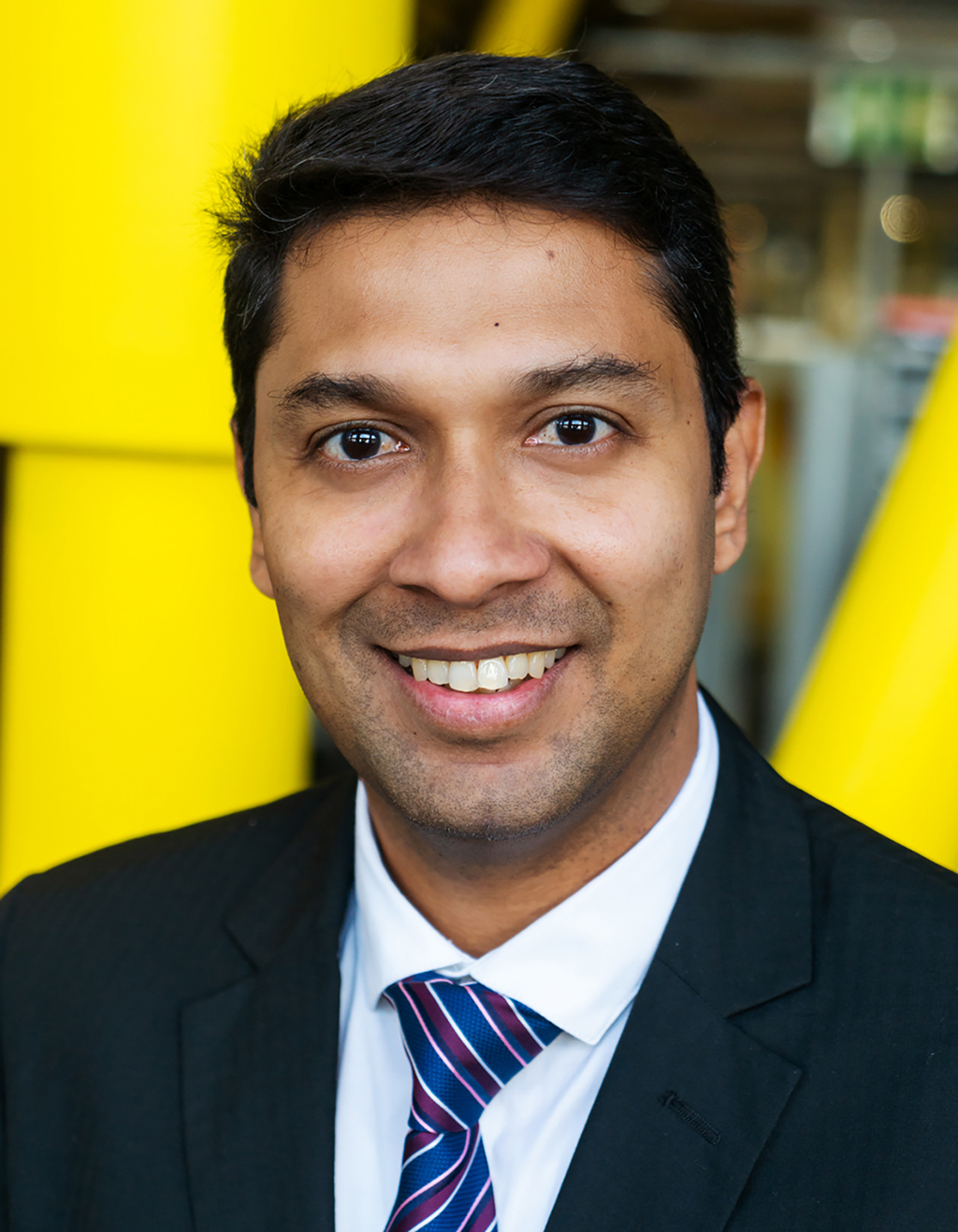
Their founding principle is to look for the most complex problem available – handed down to them by the founder Gunter Blasé – still holds the company in good stead even today. Be it Igus GmBH or its wholly-owned subsidiary, Igus India – the company thrives on providing solutions in plastics for various industries including automotive.
Igus works with engineered plastics that are basically thermoplastic alloys with fibers and solid lubricants in them to improve mobility of parts. The company’s success lies in its composition that makes plastic automotive parts highly reliable with numerous advantages when compared to conventional solutions with metals.
Deepak Paul – Managing Director, Igus India shares: “We work with engineering products, machines, and equipment in the automotive domain apart from catering to most other industries too. The whole idea is to offer the best cost-to-performance ratio to our customers and it translates into availing them the cheapest solution that works.”
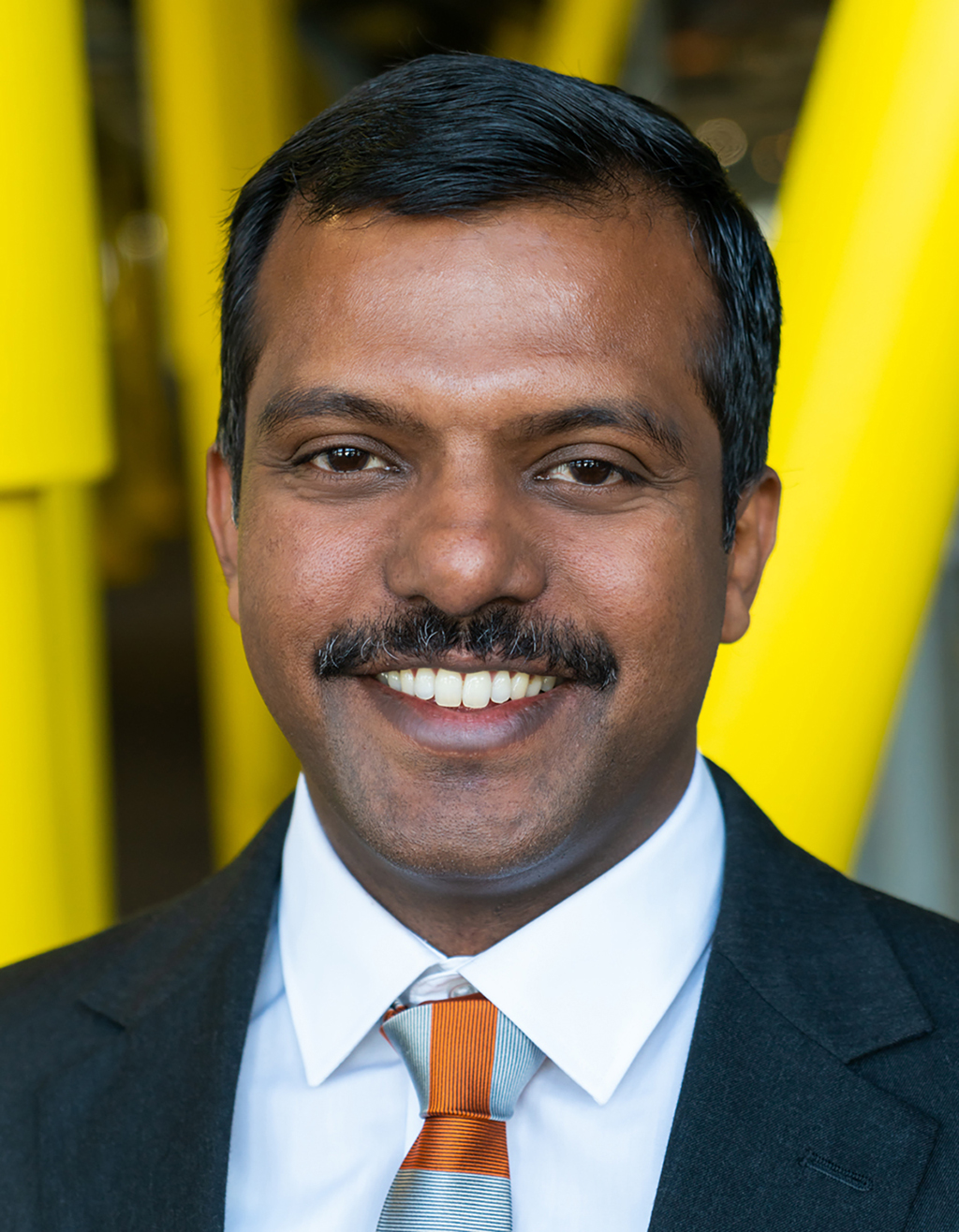
Santhosh Jacob – Country Manager and Director, Igus India says: “Our penetration into the market has happened with us offering solutions to customer problems that could not be solved using metal parts. Though, usually, customers approach us with problems, there are times when we also identify pain points and offer motion plastics as solutions. And these are arrived at after extensive field trials.”
Igus India recently launched its virtual show booth – Igus Motion Plastic Show or IMPS – exclusively for its customers in the Indian subcontinent. With an investment of about Rs. 2 million put into the virtual booth, the company welcomed their customers to experience new service offerings, benefit from global insights, and also interact with global product experts.
Engineered Plastics for Automotive Domain
Igus manufactures motion plastics in their highly automated and extensive production facility in Cologne, Germany. The facility holds the record of ‘having the 2nd highest number of machines for injection molding under one roof’. When it comes to the automotive segment, Igus has been catering to the tipper segment in India for long and in a big way where the company provides bearing solutions for various applications including seating systems, coolant pumps, brake boosters, pedal systems, door hinges, windscreen wipers among others. For instance, iglidur plain bearings in vehicles offer a variety of benefits like cost reduction by 40%, up to 80% reduction in part weight in vehicles, noise reduction, self-calibration and flexible installation concepts.
Deepak explains: “Plastics can be used in high load applications on vehicles. For example, a mining tipper is supported by 2 plastic bushes of 260 diameter which can take on a rated load of 40 tonnes of, say, slurry. These bushes work smoothly without any use of lubrication. We have applications that have now been running for almost 2 decades and some of them are the most highly use-abuse sort of applications in harsh conditions. This is an example of the strong base on which we make our product offering.”
Santhosh adds: “We have a large variety of materials and each application demands different material. For example, we manufacture various parts – from hinges, gearboxes, pedals to suspensions. Wherever there is a round metal part being used, we are able to replace them with plastics. For us, the scope of business is high.”
Over the years, Igus officials swear to have witnessed a sea change in the way automotive customers perceive plastic products for their vehicles – moving from plain disbelief in the ability of plastics to move vehicle parts to the company making more than 10 million parts in a month for the Indian automotive industry alone.
Deepak elaborates: “We have a full-fledged industry vertical that supports automotive alone with regional teams, and the supporting product group. The overall exercise of development activities in India is intensive. When we talk about the design aspect, it is complex for Indian automotive needs, and that is also where we have been largely successful because we make our products highly safe and offer consistent solutions that work reliably in any environment.”
Point of Differentiation
Igus stands head and shoulders above the rest in the market due to their technological knowhow. The company has been conducting 10,000 tests every year for the last 3 decades.
Jacob shares: “For us, plastic compounding is the core of our knowhow. We work on improvements by executing tests and working on various applications which are buttressed by the massive test data collected. And we have made the software and the data available to the customer on the web.”
The company is armed with more USPs and each is built around customer-specific applications.
Deepak shares an example: “Large commercial vehicles like trucks, for example, are built for high load carrying capacity and the owners wish for them to not require frequent lubrication while simultanesouly being non-corrosive. Besides, typical and frequently sought features are low wear and tear, low noise and lightweighting. So, each application is dealt with a different strength it needs. Possibility with plastics is that it can be molded into special shapes, sometimes few parts can be combined to be put into single piece.”
Santhosh says: “Another point is that the engines are becoming more silent which means that this will increase the possibility of polymer bearings being used. For example, we have solutions for rattle-free applications where the tolerances can be wider, and the bearings will compensate because of the specific design.”
Offering Customized Services
It is only natural for Igus to offer customized services to help customers resolve their specific issues. And the company is equipped with methods for initial trials for helping customers with optimization. Igus is also adept at 3d-printing a part using SLS (selective laser sintering) for which they have special materials at their disposal.
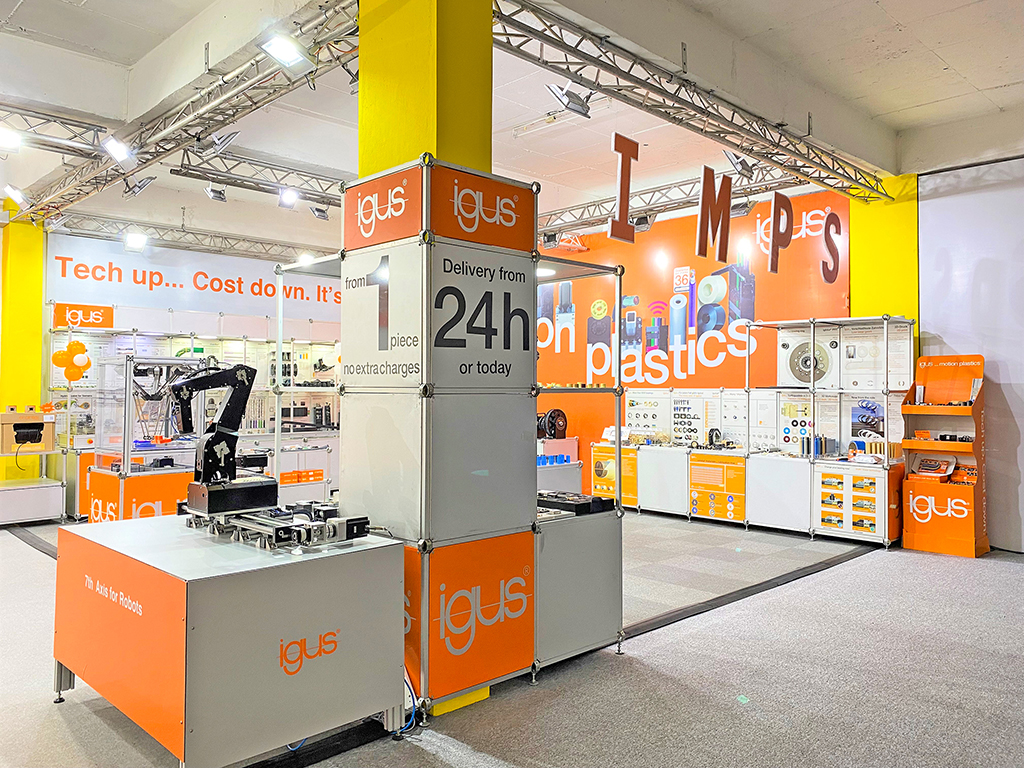
Santhosh adds: “These materials offer upto 95% similarities in behavior like an injection molded part, while promising a similar lifetime. In the last few years, we have been offering 3d-printed plastic tools using mold of Igus material to produce 10-20 pieces for customer-specific needs. And the time consumed is merely a week or less. In today’s automotive world, vehicle development time has come down from a couple of years to rolling out a vehicle in 6 months, besides which they also want faster validation. It becomes possible to get a faster feel of the product with our 3d-printed molds, parts and also machined parts and this includes testing.”
Igus boasts of going up to beta-level testing with parts. The company’s highly automated production facility in Germany manufactures at a competitive price for the customers around the world. Back home, Igus boasts of a total turnover this year of about Rs. 150 crores with automotive domain contributing to roughly Rs. 22 crores.
Looking Forward
Improving what moves with a plastic-centric approach has always been Igus’ sole driving force and today, it has grown to become a billion-dollar company with sustainability as a strong point in their psyche. As per Deepak Paul and Santhosh Jacob, disruptions will come but any vehicle will still need moving parts which can be improved with motion plastics.
And, as on today, there is none to compete with Igus India when it comes to motion plastics!