The non-ferrous metal giant has launched India’s first all-aluminium 34-foot freight trailer, which is 50 per cent lighter and weighs over 2.5 tonnes less than an equivalent steel trailer. Dhiyanesh Ravichandran gets ahold of the team behind the conception, fabrication, and testing of the all-aluminium (AL) trailer to ascertain the advantages of AL over steel as a manufacturing material, its operational benefits in trucking logistics, and emerging avenues for the metal in transportation and automotive industry.
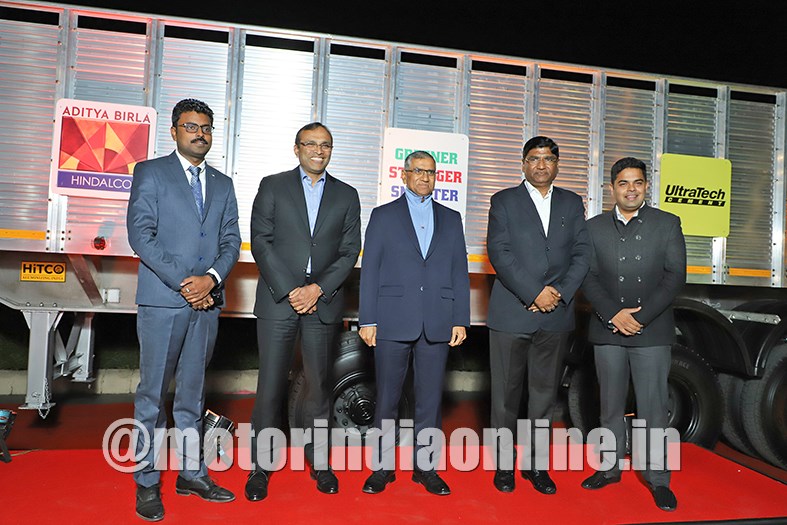
What comes to your mind when asked to name a ‘strong metal’? ‘Iron’ is likely to be your instantaneous answer, although you will be surprised to know that pure iron is quite soft. That’s perhaps why it is combined with alloying elements to make ‘steels’ with higher tensile strength for its common use in various civilian and industrial applications. Now, what is the mental image you bear when you think about Aluminium? A foil paper or pop can? Don’t blame yourself, that’s perhaps the reputation that AL enjoys in our common everyday parlance.
What we conveniently forget is that AL is also almost always alloyed to enhance its yield strength as much as steel, and is predominantly used in heavy industrial and civilian applications including transportation. Aluminium is the mainstay raw material in aviation, shipping, railways, and commercial vehicles to name a few. Not just the pressure cooker in your kitchen that withstands enormous temperature is made of aluminium, more than 60 per cent of the structural weight of an Airbus A380 – world’s largest passenger airliner – as well as the superstructures of cruise ships and TGV Duplex trains or your everyday metro coaches also owe their existence to AL!
The first AL-made truck tankers, tippers and load bodies arrived way back in the 1950s in the Western world, and today, most of the semi-trailers are made entirely of aluminium. Owing to its low density and durability, the AL alloys are preferred in all these applications, thereby making the vehicles lighter and efficient to run. Yet another boon with this metal is its resistance to rust and corrosion, which extends the life span of vehicle bodies way longer than that of steel. However, in developing countries like India, the steel holds sway in truck bodies due to its lower cost and long-established legacy, and the transition to AL would warrant a fairly tough jumpstart.
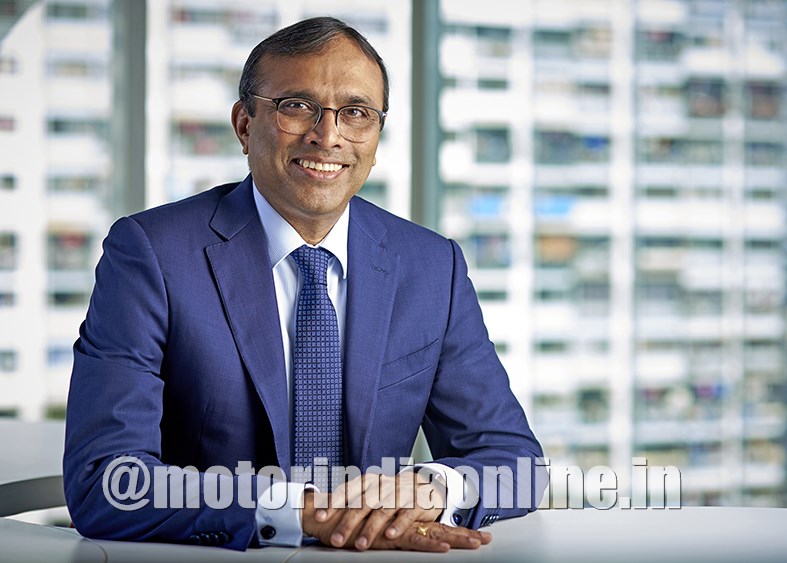
Aluminizing India
“Well, we at Hindalco are all-set to give that big push required to ‘aluminize’ the Indian logistics and freight industry”, proclaims Satish Pai, the Managing Director – Hindalco Industries Ltd. A subsidiary of Aditya Birla Group, Hindalco is one of the leading producers of AL and has always been exploring new business cases for its non-ferrous metal. It now finds a huge opportunity in truck transportation, especially with trailers in the immediate future. “It is indeed the very merit of aluminium that makes it a perfect engineering and sustainable solution for haulage applications. It weighs just one-third, but aluminium alloys can be as stronger as steel. It demands less maintenance and care, offers a longer life span, and the metal is one-hundred per cent recyclable”, he notes. He also emphasizes that high-quality ‘5-series’ aluminium-magnesium alloy has gone into its making of the trailer, a similar grade metal that finds its relevance in various defence and marine applications.
This isn’t something new for his company. Hindalco’s fully-owned subsidiary Novelis is already engaging the automotive and transportation industries across the globe with aluminium. The MD says that his company is leveraging the knowledge and expertise of Novelis in this regard and based on the domestic market standards and customer demands, AL alloys that go into the making of trailer bodies are developed. “Our strategy is to start ‘Aluminization’ mission with bulkers and trailers, as cost-benefits of light-weighting is more viable in commercial vehicles than other segments. EVs are yet another potential area, but they are likely to take some time”, he adds.
Early last year, Hindalco launched the first aluminium bulker designed for dry bulk cargo. Satish Pai points out that after its successful commercialization, the next step as a natural corollary was to go for a trailer unit fully built of aluminium including the chassis. “With this product development, we have covered almost all sub-segments in dry-bulk haulage. Considering an estimation that about 20,000 trailers are fabricated every year in the country, even a 50 per cent adoption would mean a huge turnover potential of over INR 500 crores for our company”, he averred.
Right metal for trailering
Early last month, at the launch event of AL trailer in Jaipur, Hindalco’s Senior VP (New Business and Product Development) Sagar Dhamorikar and Sudhir Jain, Assistant GM (Market Development) illustrated AL’s higher strength-to-weight and stiffness-to-weight ratios and lower modulus of elasticity as against steel, along with the natural formation of the oxide layer offering excellent corrosion resistance – even eliminating the need paint finish – all working in favour as a superior construction material for trailers. Jay K. Mulchandani, MD of Core B Group – a leading trailer fabricator in the city – joined the interaction. He is also the managing partner at Hindustan Trailer Corporation (HITCO), a newly established firm to manufacture fully-built all-aluminium trailers for the domestic market, with active support and patronage of Hindalco.
Having spent months in the fabrication of trailer, Mulchandani revealed that a “This project was quite challenging, cutting and welding processes in particular, but turned out to be a big revelation for us in infusing long-awaited innovation into trailer manufacturing”, he said. The trailer boasts a modular design architecture, with rolled plates and upper body developed by extrusion techniques. The chassis part, he commented, was yet another critical area of fabrication and has turned out to be very strong, while being compliant to ARAI inputs and engineering parameters. “With chassis in AL successfully pioneered, the avenues for any other upper body iterations such as tankers or tip-trailer bodies is now open”, he opined.
The strenuous processes of aluminium welding have warranted addition expertise. Fronius India, a subsidiary of Austria-based Fronius International that is into welding technologies, was roped into the project, with whom Hindalco has an MoU to develop effective AL welding techniques for auto and transportation products. Said its Managing Director, V.V. Kamath: “Although we supply welding systems and expertise for AL welding in passenger vehicles in India, the AL trailer was a bit challenging. For instance, the welding thickness has to be as minimal as 2 mm while making fuel tanks for two-wheelers, but in the trailer’s case, the thickness extends beyond 8 mm. Moreover, the penetration has to be flawless, as AL is very susceptible to blowhole formation and dependent on various external parameters like temperature and cleaner air matters for effective welding”.
Superior value-proposition
Testing and on-road trials of the AL trailer were done at the hands of Kamal Exim Private Ltd., a trucking fleet catering to textile, chemical and cement logistics in the region. “I excitedly undertook the trials for several months, despite having no idea about AL trailers. Being associated with Aditya Birla Group for about 13 years, I had immense confidence in Hindalco”, claimed its founder and MD, Gagan Maheshwari.
He listed out various performance parameters that were given due importance during the trials, including its abilities to withstand the stress of trailering and road handling across a variety of load and road conditions. “Notably, my usual operations include haulage of liquid chlorine gas cylinders weighing 1,500 kgs each, whose tricky handling may damage sidewalls of the trailer. In AL trailer’s case, the support system given to all-aluminium sidewalls rendered it stronger and we faced no issues at all”, he claimed.
As a fleet operator, Gagan feels that the AL trailer makes a great value proposition as against a similar MS (mild steel) trailer. Firstly, he argues, an additional payload of 2.5 tonnes for every trip and savings out of extended fuel and tyre mileage would make a huge difference in the long run. Secondly, there is no need for frequent body maintenance and paint job, which again is a big saving. Thirdly, the average lifespan of the MS trailers is around 5 years, while its salvage value for metal is hardly 10 per cent of its original cost, thanks to corrosion. On the other hand, AL trailers can easily last for 20 years, after which the metal would still command 70 per cent value when scrapped. That way, the additional cost of the AL trailer can be recouped in less than two years, while also commanding higher resale value, he opines.
Drivers involved in the trial runs of the trailer have reported a smoother tow with AL trailer, even when loaded, as against MS trailers. Jay Mulchandani claimed that higher energy absorption ability of AL also demonstrates better crashworthiness with limited damage to vehicle, occupants, and cargo, thereby enhancing road safety. Further, he asserted that an articulated truck can save 600 litres of diesel over 1,00,000 km if the vehicle is lighter by just 1 tonne. In other words, each kg of AL used in the truck saves 26 kgs of CO2, which can greatly complement emission reductions out of BS-VI standards.
Trailer kits for mass-adoption
The fabricator is working on a mass production facility for AL trailers in Jaipur, which can expand his capacity to 300 units from 50 units per month at present. “Considering the size of the trailer market in India, there is likely to be a huge gap between colossal demand and finite supply of AL trailers”, Mulchandani pointed out, while hinting at a phenomenal opportunity set in place for trailer fabricators in the country. It is in this regard, Hindalco has come up with the concept of modular all-aluminium trailer kits to offset the supply gap. The trailer kit consists of two main high beams, eleven middle crosses, one fifth-wheel plate, and a complete upper tray including side channels and walls. Targeting fabricators from across the country, the company also vows to provide all necessary expertise and engineering assistance for the assemblage of the AL trailer, thereby pushing for faster adoption of AL trailers in the local market.
With aluminium bulkers and trailers set in motion, the bottom line is that Hindalco is establishing aluminium as a superior construction material for trailers and truck bodies. “We have already initiated our ‘Maxloader’ brand of all-aluminium container load bodies for intermediate and medium-size trucks. With the latest developments on the trailer side, our focus is now on developing AL oil tankers. Trucking apart, the next segment that we are betting high on is that of buses, wherein we are developing the complete superstructure and side panels out of aluminium, which can be a game-changer for electric bus architecture”, affirmed its Managing Director.