Considering the low levels of training in the automotive workforce, including the segment of component manufacturing, it is imperative to reorient skill development initiatives and institutionalising lifelong learning as part of the industry culture, says Nikunj Sanghi, President, Automotive Skills Development Council (ASDC) in this guest column
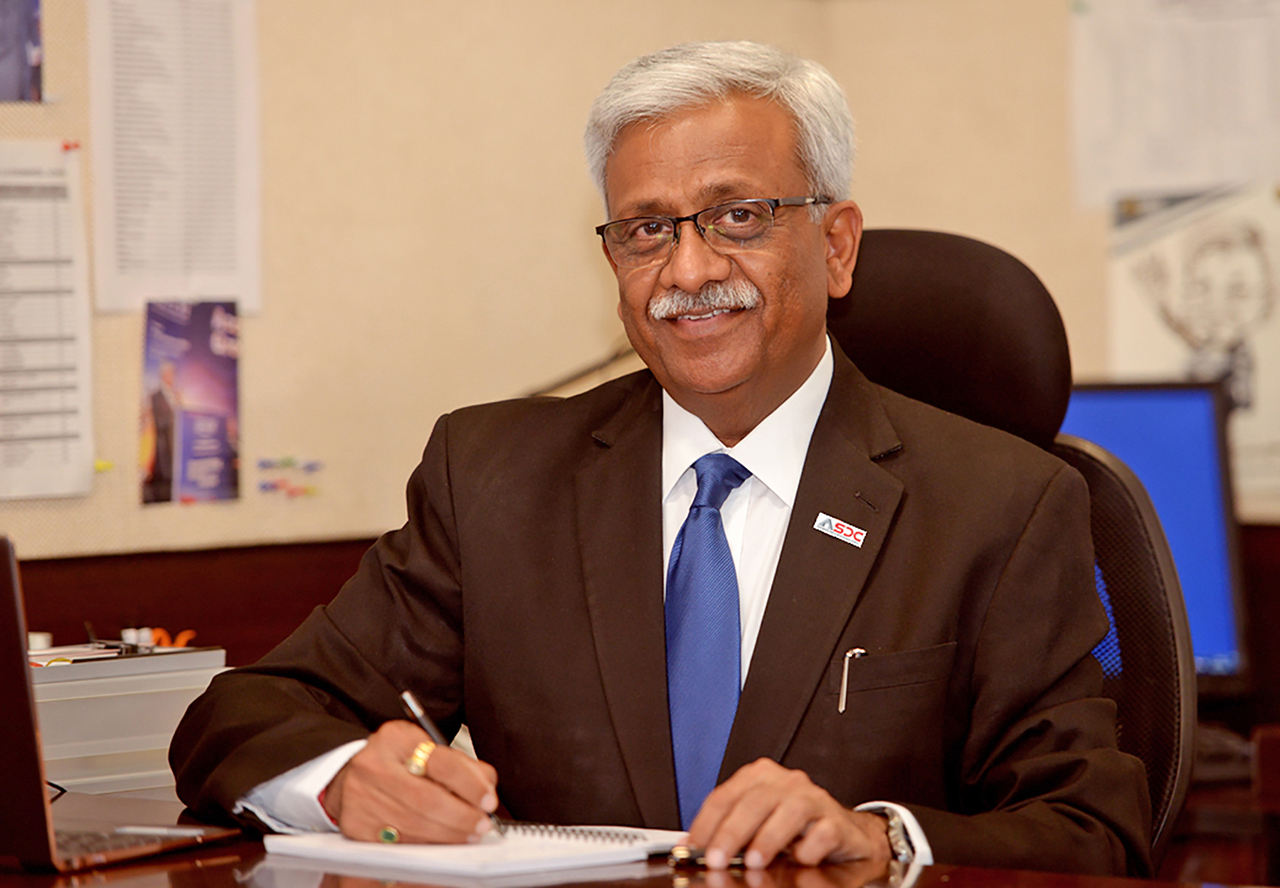
As one of the fastest growing markets worldwide, India’s automotive sector contributes majorly to the nation’s manufacturing ecosystem. It also accounts for around 7% of the country’s overall GDP while employing 32 million people, making it one of the largest creators of employment in the non-agricultural segment. However, technological and structural changes confronting the industry are a major challenge in ensuring its human resources are ready to keep pace with the market changes. Moreover, the advent of Industry 4.0 and the emergence of electric vehicles (EVs) remains one of the fastest rising global phenomena for the sector.
Skilling Shortage and Implications
Here, the skilling challenge comes to the fore since the skills required for servicing EVs vastly differ from the legacy skills used in manual vehicles. As the automotive sector seeks to transition towards an Atmanirbhar Bharat or self-reliant India, it has to address this skills gap, particularly that of its blue collar workforce. Given that skilling courses must cater to both existing employees and the future workforce, retraining is vital in upgrading skills and making workers more industry-relevant. Industry 4.0 first highlighted the paradigm shift in manufacturing while triggering an irreversible transformation in the structure of automotive jobs.
Whereas the importance of making the workforce future-ready is apparent due to this transition, the pandemic has made this more critical, considering the evolving nature of jobs controlled by technology. Sub-sectors like automotive components and vehicle servicing are now poised to experience the most impact on their jobs from trends such as mechatronics, vehicle electrification, autonomous cars, and the like. A shortage of skilled workers is already being felt in the industry. For example, while road transport sub-sectors and dealerships have the most demand for jobs, they are experiencing the maximum shortage of skilled human resources because of the inadequacy of supply side institutions.
Thanks to the periodic introduction of novel models and technologies, industry players need to ensure constant re-skilling and up-skilling of workers. Furthermore, new roles are necessary to retain the relevance of workers and ascertain companies maintain sustainable growth and market competitiveness. Fortunately, the Centre remains cognisant of the skills gap. Accordingly, in collaboration with Automotive Skills Development Council (ASDC) and other industry bodies, it is implementing multiple skilling initiatives.
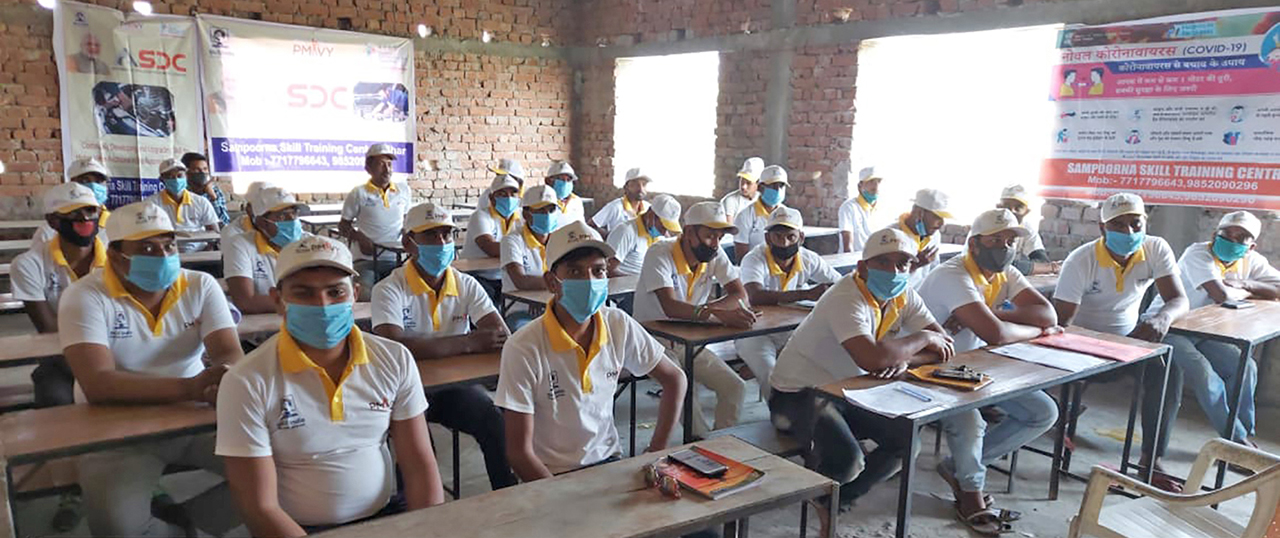
This includes investing in human resource-intensive frameworks such as Pradhan Mantri Kaushal Kendras (PMKKs), apprenticeship schemes like National Apprenticeship Promotion Scheme (NAPS), micro-entrepreneurship programmes and encouraging start-ups. Nevertheless, more needs to be done to address the huge skills gap. For instance, the Centre can focus on specific sub-sectors of the industry that can catalyse higher jobs generation, undertake structural reforms in education and skilling for fostering a robust Industry 4.0-compliant workforce and promote conducive policies facilitating faster use of smart manufacturing practices, among others.
Likewise, the industry must get its act together by rapidly re-jigging operating models keeping smart technologies in mind to maintain competitiveness and drive large-scale re-skilling of its workforce. A collaborative relationship between the sector, the government and industry associations is imperative if the workforce is to become future-ready. In the context of rising automation, workers can be reassured that this does not mean their jobs will be automatically replaced by automated processes. Automation can be beneficial for workers performing hazardous tasks. Automating these processes improves the overall safety of workers and boosts product quality via standardisation, which makes the process extremely efficient and precise.
Retain Relevance or Risk Redundancy
Since automation and the deployment of robots are steadily rising across industries worldwide, it’s in the interests of workers to opt for upgrading their skills to work alongside robots or risk redundancy in current roles. Upgrading or relearning skills is especially important because of the shift from legacy powertrain technology to electric or autonomous vehicles. While an internal combustion engine (ICE) model has almost 2,000 parts, an electric engine only has about 20 moving parts. Although the EVs are easier to maintain, workers require different skill-sets to service such cars.
EVs will act as major market disruptors, leaving an impact on the type of job roles available across the entire automotive value chain. Conversely, the ascent of new technology will affect the workforce in other ways too. It will augment the number of high-quality jobs, witness employment arising from the development of allied infrastructure and in human resource maintenance. Naturally, the current workforce will have to be re-skilled to avoid redundancy. The mix of workers at automotive component manufacturers and OEMs will also undergo a profound impact as technological changes due to Industry 4.0 impact workers by transforming the demand for skills and the job mix.
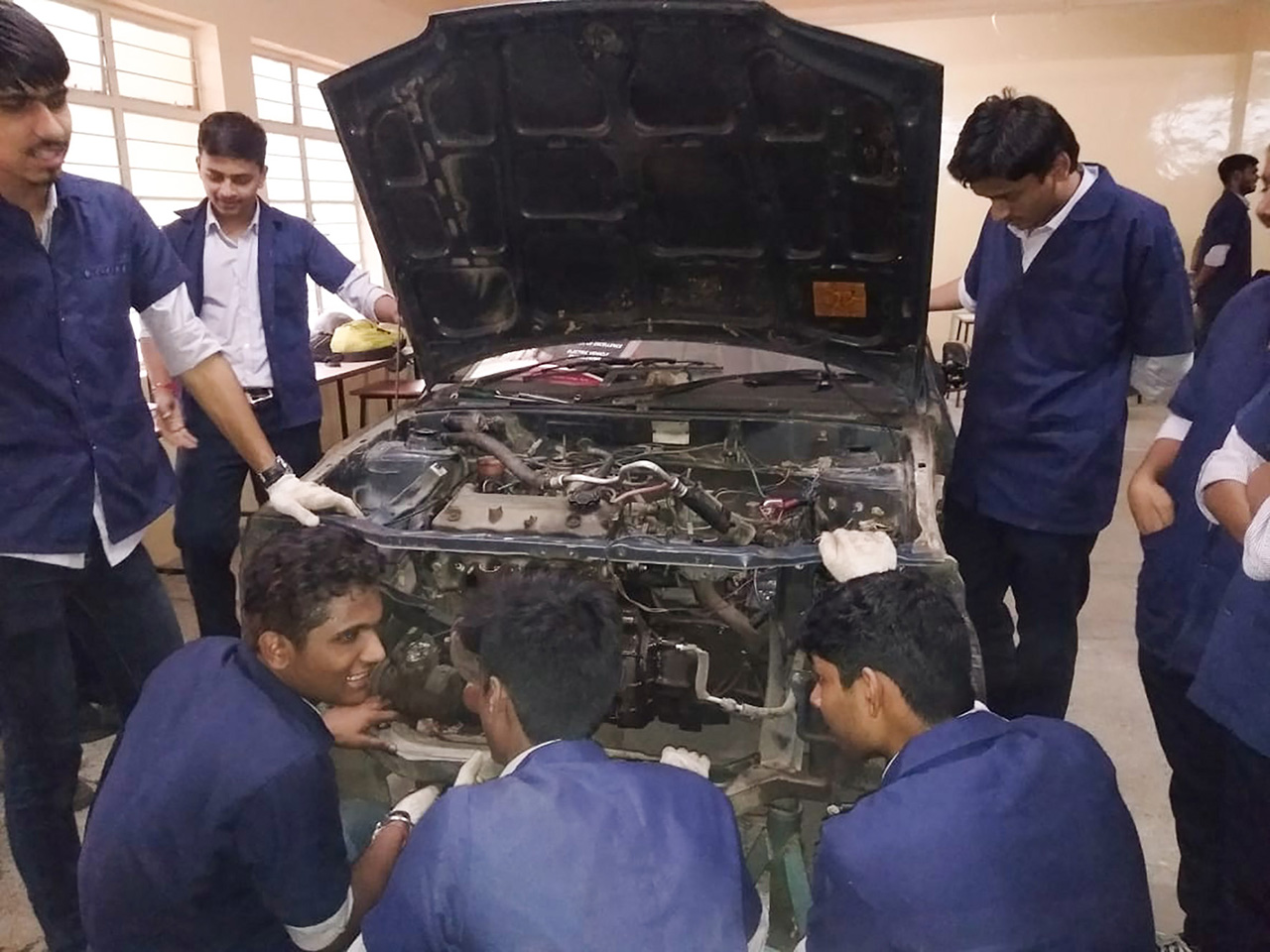
Consider the dealerships segment. The concurrent rise of digitalisation and burgeoning cohorts of millennials are changing the automotive sales experience. As a result, tech-savvy salespersons apart, soft skills are gaining prominence. Today, an enjoyable customer experience and catering to personal needs are crucial to prioritise retention and relationship management. Simply selling vehicles to customers will no longer win the day. These employees also need to act as trusted advisors for customers. Besides being trained in the nuances of connected cars and EVs, the dealership team must be brought up to speed on personalising the purchase journey of customers. In such scenarios, soft skills are paramount. Therefore, all customer-facing employees should be imparted soft skills training to boost customer satisfaction. Along with higher sales conversions, it promotes greater customer satisfaction.
Apprenticeship Programmes
Meanwhile, the faster pace of technological changes and the changing pattern of consumer demand are raising the likelihood of greater skill gaps among workers. In these situations, analysts believe apprenticeship programmes could help in meeting some requirements of automotive companies. Currently, apprenticeships are only prevalent among OEMs and automotive component manufacturers in Tier I and II regions. Since such apprenticeships are driven by dealer demand, the chances of skills mismatch between what is taught and the workplace requirements are remote, unlike when similar training is offered in schools, polytechnic courses and industrial training institutes (ITIs).
The NEP 2020 provides that even students of middle level shall be exposed to hands-on training in vocational skills like carpentry, plumbing, electrical repairing, horticulture, pottery, embroidery, etc. The policy has set the target of providing vocational skills to at least 50% students by 2025 in such a way that the vocational skills acquired at school level may be further extended up to the higher education level, depending upon the requirement of individual students. Unfortunately, the apprenticeship programmes of these industry players are disassociated from those offered by the government such as NAPS (National Apprenticeship Promotion Scheme), NEEM (National Employment Enhancement Mission) and EETP (Employability Enhancement Training Programme), among others.
As dealership sales and services, which are major employment generators in automotive, remain wholly oblivious to these apprenticeship courses, the scale of such programmes should be expanded through public-private partnerships. This will provide more workers with a better opportunity to enter the segment through formal employment avenues. Going by the dynamic and evolving nature of automotive manufacturing and other segments, industry players believe the focus should shift from formal training of colleges and academic institutions to one of lifelong learning, re-learning, re-skilling and up-skilling. Since technological disruptions are a constant feature of our modern manufacturing era, skills learnt during graduation and post-graduation years quickly become outdated.
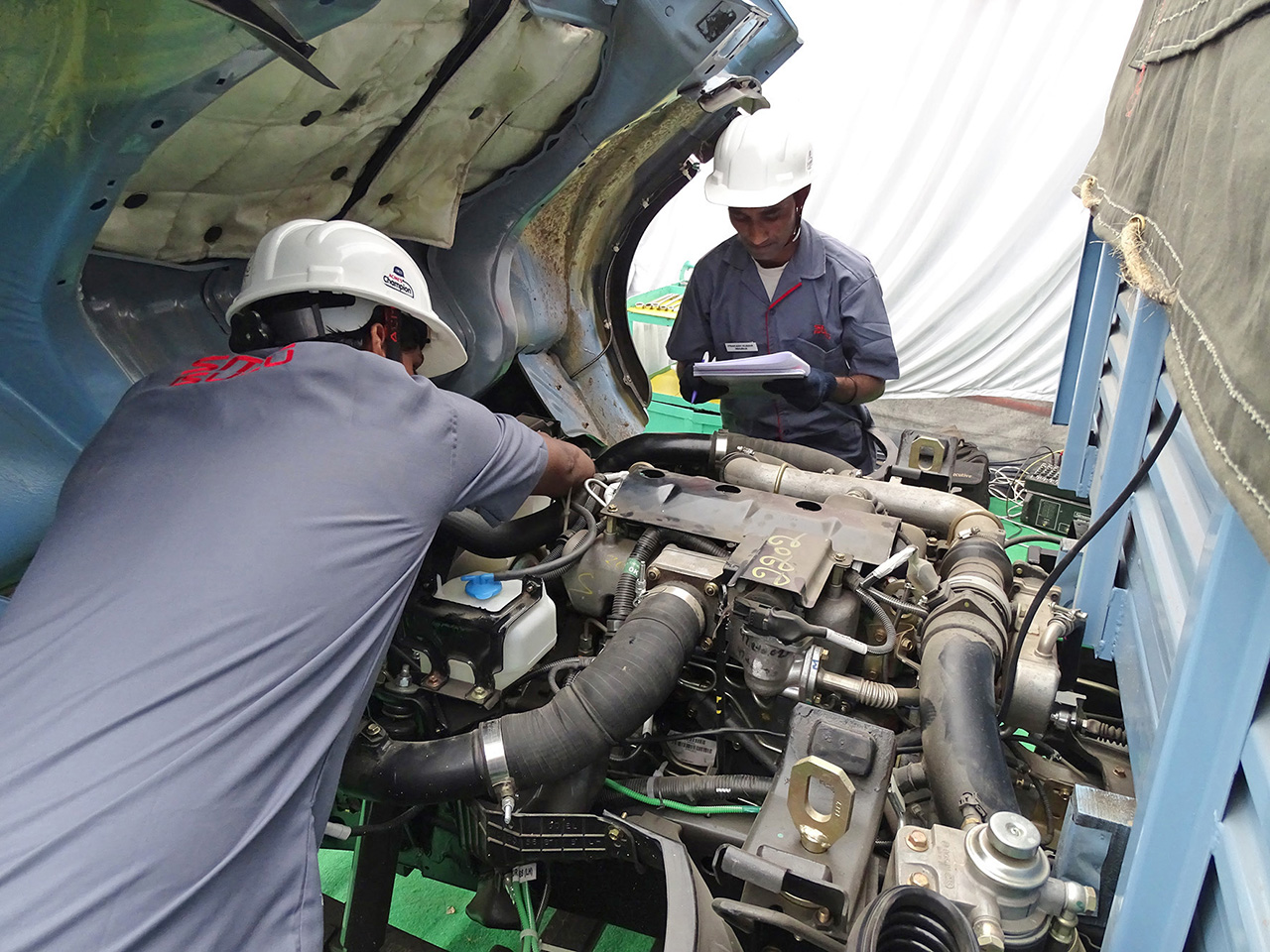
Periodic Training and Gender Diversity
To overcome this lacuna, training plus learning and development programmes have to be undertaken periodically to ensure relevance. Consequently, the sector is evincing renewed interest in re-skilling and up-skilling of the present workforce across segments. Many initiatives are aimed at fostering a culture of lifelong learning within the workforce. This will enable workers not only to upgrade skills but even permit them to take up more valuable roles if they possess specific skills. Stakeholders across the spectrum speak about the need for workers to be imparted high-quality skills training, including in domains such as advanced problem-solving and analytics.
An analysis of the supply side of the industry indicates that companies primarily meet their workforce requirement via higher education, technical and vocational training as well as the NEET (Not in Education, Employment or Training) segments. Broad interactions with dealership sales and services players, automotive component manufacturers and transport fleet operators reveal that the existing skilling infrastructure is severely constrained and cannot meet current demand. For policymakers, sectoral players and industry bodies, a compelling case exists to develop skilling capacity for the NEET segment, which comprises a major proportion of the sector’s supply base.
There is another aspect automotive players must address. As companies in varied verticals focus on greater gender diversity, a high degree of segregation is noticeable in the industry – horizontally and vertically. Typically, female employees work in white-collar roles across research and development and human resources. Another area where women witness a sizeable presence is at dealerships. Where the shop floor is concerned, most companies have virtually no women. Nonetheless, a few large OEMs have established assembly lines only with females. Skilling programmes could also target women to enhance their chances of finding gainful employment in the automotive sector. Additionally, the authorities and industry bodies can provide targeted enabling structures supporting women’s participation in automotive. Shortfalls in skilling gaps could be addressed by establishing targets for ITIs and other skilling entities to increase women’s participation in courses teaching technical and mechanical skills. With the sector undergoing a sustained phase of transformation, promoting greater gender equity and better lifelong skilling opportunities for all workers will help the sector emerge as a global automotive manufacturing hub. When this happens, the vision of a self-reliant automotive industry will finally be grounded in reality.