In an exclusive interaction with Nikunj Sanghi, Chairman, Automotive Skills Development Council (ASDC), N. Balasubramanian finds out how ASDC is revamping its efforts to become an organization to reckon with globally in the automotive industry. He shares that skill gap is not only being faced by India but across the globe. India, though, has the demographic advantage which if worked to a benefit can make it a hub for the world. Efforts are on where a Skilled India is an AatmaNirbhar Bharat!
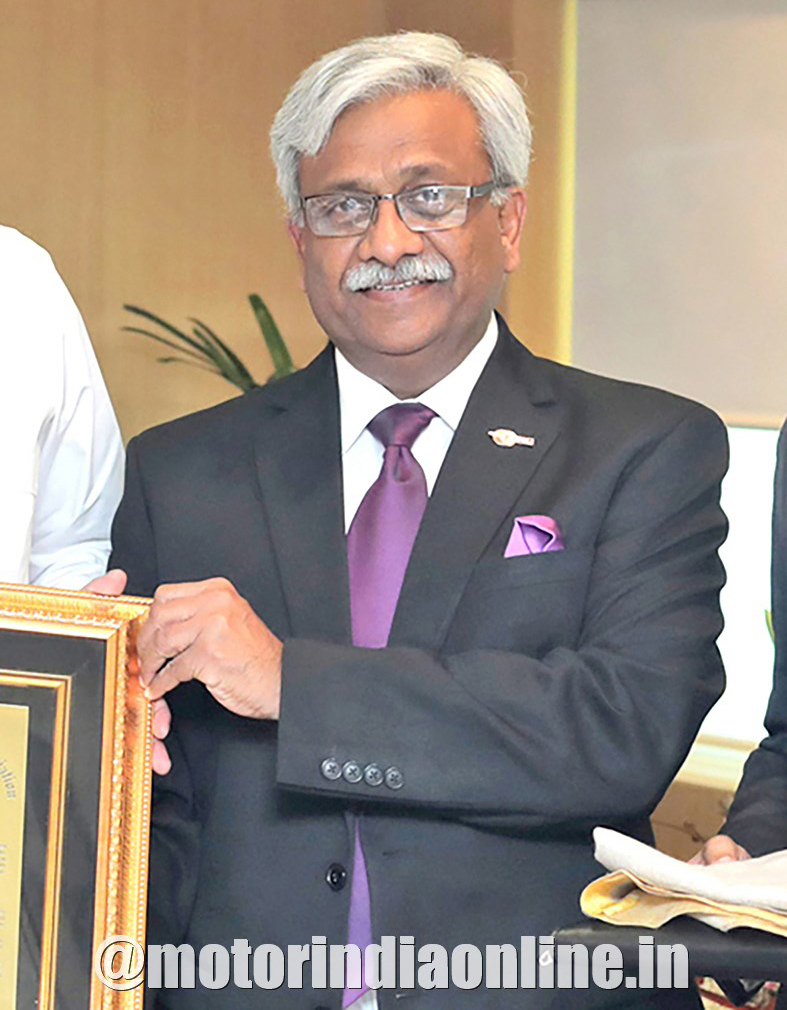
Excerpts:
How, in your opinion, is the COVID pandemic impacting the Indian automotive industry? How is ASDC planning to help the industry in the current situation?
Due to COVID, the Indian economy is staring at negative GDP points standing at 6.8. The automotive industry is worse hit because it works on positive sentiment and COVID has further dampened the spirits. The impact of the pandemic can be seen across the value chain – from the component and vehicle manufacturers to dealerships. The last two years were about growth phase because of which most of the stakeholders were into an expansion mode. Naturally, costs were high and so were overheads. In India, vehicle penetration rate is among the lowest in the world making it highly fertile for a growth opportunity, especially where almost every brand from across the globe wishes to bring their business to India.
From the skilling aspect – COVID has rendered many people jobless. Labourers have migrated back home and there was no way that the manufacturers could hold back the skilled labour. This has changed the way we do business. It means that the entire landscape of skilling has also changed. The skill space cannot remain vacant for long for which we must align ourselves to the new requirements of the industry. And ASDC is working towards it.
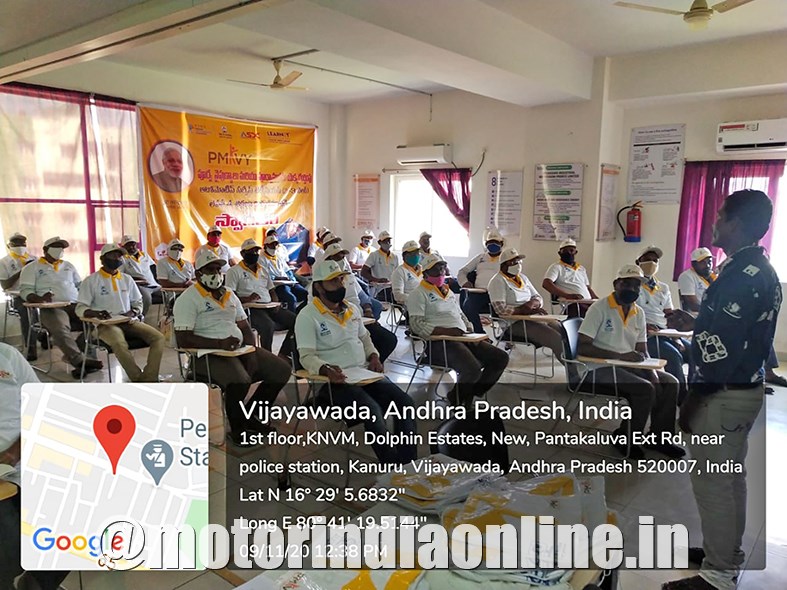
What are the key areas in the auto industry where there is a current and emerging skill gap, from the AatmaNirbhar Bharat perspective?
We need to become globally competitive to become ‘AatmaNirbhar Bharat’. The Prime Minister is talking about Make in India for the World. In that context, it means quality needs to come in and possess highly skilled manpower who would deliver first time right and first time perfect. It is only then that when we can reduce costs, and make India a destination for global procurement. And that is the gap we need to fill as early as possible.
What are the major skill gaps that exist in the auto industry currently? What are the expectations from different stakeholders to handle and bridge this gap?
Firstly, there is scarcity of skilled labor specifically in the manufacturing side because of the migration of the labour. Also due to the absolute erratic demand pattern in the auto industry, a majority of the workforce is hired on contract depending upon the capacity and the demand. Most of the workers who have migrated are unwilling to come back creating a huge skill gap. Both the government and the ASDC are in the process of identifying the location of the ¬migrant labour and to create a platform where we start matching employers and workers.
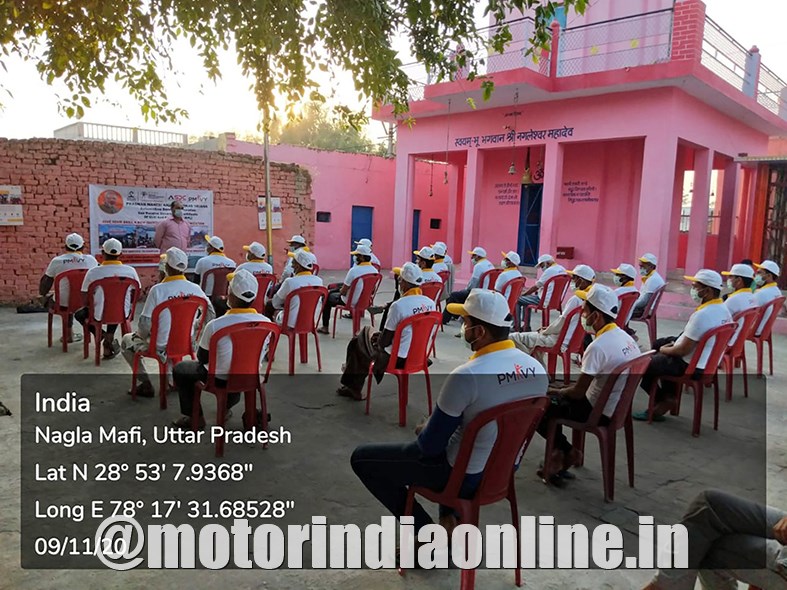
Secondly, training and skilling fresh candidates under the National Apprenticeship Promotion Scheme (NAPS) launched by the government will be a big help because this will help the employers to not only train and skill people on the job, but also to reduce their manpower costs drastically and once they are skilled to give them permanent employment. ASDC is reaching out to the industry making them aware of how NAPS functions seamlessly and how big is the fiscal incentive that the manufacturers have if they enroll themselves with the NAPS. The Scheme is from 6 to 18 months, and there is both a cash component for the training period and a monthly subsidy that is given by the Government of India, which is administered by the sector skill councils.
Another focus area of ASDC is skilling people in technologies such as machine learning, artificial intelligence and those required in the after sales sector which is digital learning entailing servicing the customers digitally. The digital importance came in before COVID, but has been accelerated due to the pandemic as there are no physical test drives to the extent that over 80% of the purchase and the accompanying experience must be done digitally. In the COVID period, we have launched at least 5 programs with digital online learning platforms, which would upskill and reskill existing manpower at the dealerships.
Finally, the EV space is another gap that we need to fill. We have recently launched another online fully-digital platform in EV engineering. Going forward, we will be continuously working on developing digital content.
How do you think the industry can insulate itself from such a scenario arising again?
Even pre-COVID, vocational training was deemed the way forward. The entire focus of the present educational system started changing to include vocational training from as early as the eighth grade of school. What ASDC is definitely doing is to try and develop content at that level and take it forward, start working with various skill universities, which are now coming up and with increasing recognition by the government courses like Bacherlor’s in Vocational Education has become a recognized degree. The industry can hire people from vocational training instead of just purely academic background. These degree holders are productive from day one and are already trained to do the job. This will eliminate any skill gap in any unprecedented scenario.
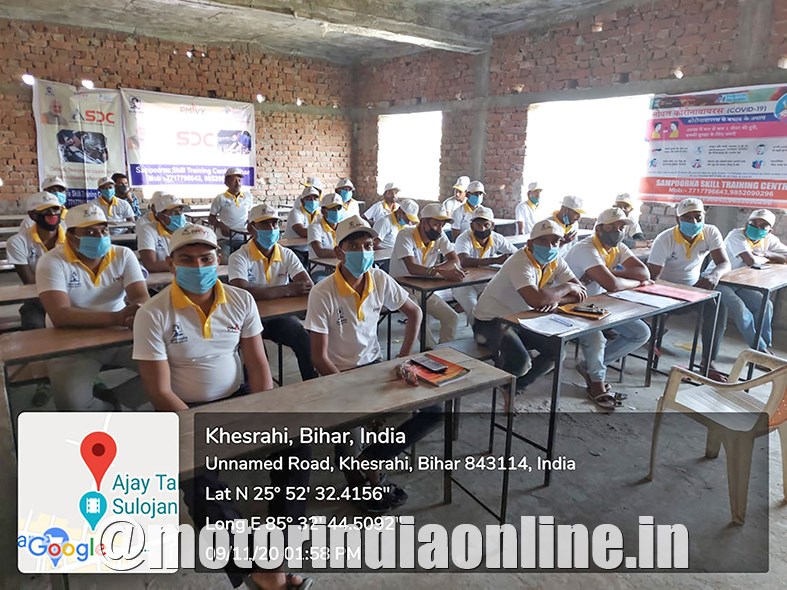
Merging of the technical education with vocational training is the other major step. The recognition is important because that is what gives the candidate employment.
How is ASDC working towards tackling unemployability of graduates in the auto industry?
Various skill universities are now coming up which would definitely meet global standards. ASDC is reaching out to various academic institutions and colleges and working with them on additional credits, which can be added to an existing course to get the student trained vocationally in areas like R&D, manufacturing, sales and after sales, which will make the student more acceptable to the industry. And since these courses will be designed by the ASDC, they will fit the industry requirements.
With the driver attrition rate about 22%, what seems to be the challenge in getting new people to get trained at the truck driver training centers?
In my view, 22% is a conservative figure and it is being felt by the industry. But things are changing in the sense that some of the new vehicle sales are happening only if the manufacturer promises to provide a skilled driver with the vehicle. Only if more respectability is accorded to the truck driver profession, only then new people will want to enter this field. There are now air-conditioned cabins and the drivers have a sleeping space inside it besides mandating the number hours of work that are required. I think sourcing is our weakest link when it comes to recruit new people to get driver training.
Tell us about the alliances that ASDC has.
ASDC realized that if skilling has to become relevant, attractive, and is what the industry wants, then ASDC certification needs to have more credibility. Our industry partners shared with ASDC that our certificate was not well accepted by the industry because the candidates were found to be wanting in the skills for which they were certified. The major gap was how they were getting certified and how human intervention was not making the assessment system as transparent and as robust as it should have been. We decided to make the system foolproof, free of human intervention, where the entire assessment process becomes credible. But it was difficult getting TCS onboard because one, their hands were full, and two, they were not comfortable working on government-aided schemes because they thought that they would have to tweak their quality to work with government-aided schemes. We set out to dispel the notion and made a business case for them to onboard with us.
Now, both the theoretical and the practical portions are assessed and tested without any human intervention which gives better credibility to the ASDC certification. The potential employee can digitally check the candidate’s eligibility for the certification he has received, the QR code, and assure himself with the skill of the candidate. We have developed Learning Hub with TCS which would be available either free of cost or at a nominal cost, so that the entire learning process can be done digitally at one’s own convenience. Another initiative that ASDC has undertaken is the digital Train-the-Trainer program and their assessment to help improve their quality.
What do you think are the key learnings from the from the global arena in skill development?
India has been sending representatives to the World Skill Competition which is akin to Olympics in sports. The last one was held in Kazan, Russia. I was there with the automotive team and the Competition was an eye opener. We realized that unless India aligns to the global skilling standards, not only will we be missing the skilling bus but that AatmaNirbhar Bharat and global competitiveness will be difficult. In Kazan, the vocational training institutes had students as young as 12 years of age, and they know that they need not be academically qualified to be employed. And to promote this culture, they allow masses of students visit the Competition and give them a guided tour where they can feel the skilling ecosystem around them. And that is where incubating talent towards skilling starts. This is the path that India needs to take. First, align our skilling standards to global standards, second, start incubating children from their school level into this skilling ecosystem. And finally, give skilling the same dignity which is given to academic degrees. Change in perception is what is needed where becoming a graduate is thought to be imperative even if the student later on does not get a job. Rather the thought process should be that learning skills to get employed, and become financially independent by making a career out of what has been learnt feels respectable. An entire cultural change is needed. Once this culture sets in, there is no way India can be stopped in becoming a hub for manufacturing, and supplier of skilled talent.