Automated trucks address several challenges that the trucking industry is facing simultaneously: hours of service, driver shortage, fuel costs and safety. Yet the economics is not very straightforward, and a rapid transition will significantly depend on regulatory push as operating cost savings can currently be reached only in few applications where a high share of truck platooning can happen, say Jeffry Jacob, Partner, and Wilfried Aulbur, Senior Partner from Roland Berger, a leading global management consulting firm.
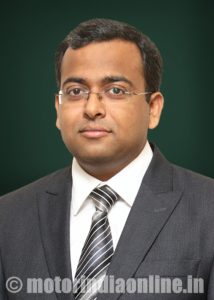
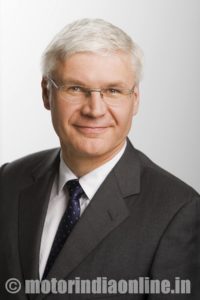
The trucking industry has come a long way from its earlier ‘avatar’ and has successfully worked towards creating safe, efficient and green trucks. This has resulted in 21% reduction in truck fatalities from 2001-13 and NOx levels have reduced by 95%, as well as led to more efficient powertrains, less rolling resistance and lower aerodynamic losses. Currently, the industry is actively engaged in harnessing big data and connectivity for more pro-active maintenance, better driver engagement and collecting real time information to help better optimise performance and design. All of these have led to significant efficiency increase in the trucking industry. The obvious question therefore is whether self-driving trucks are the next evolution in the industry.
The benefits of automated trucks are definitely quite significant with multiple benefits at both the level of the fleet owner as well as the society. Today over 90% of truck accidents are estimated to have been caused by human error. Driver shortage and retention have become critical issues not just in developed countries, but also in emerging economies such as India. The truck driving profession is under severe pressure as the new generation does not want to follow in their father’s footsteps, they do not want to stay away from their families overnight, and the pay is not seen as commensurate vis-à-vis the high stress levels. Automated driving would alleviate the situation to a large extent by increasing driver safety and comfort, thereby providing optimised driver rest periods and eliminating human error, in addition to better vehicle utilization and fuel efficiency gains for predictive driving. Cooperative automated driving could provide improved aerodynamics and further lower fuel consumption through reduced inter-vehicular spacing.
The top industry issues addressed at both the individual fleet owner level and at the societal level are highlighted in Fig. 1.
If we consider technological development towards the fully automated truck, this is expected to happen in stages. In Stage 0 the driver has to be fully engaged as there is almost no automation. This is followed by Stage 1 where individual functions may be automated, e.g., lane assist, cruise control, etc. Stage 2 is the partial automation stage where the driver can be both ‘hands-off’ and ‘feet-off’ but his eyes need to stay on the road and hence he continues to stay fully engaged. This is the current stage of technological adoption in commercial vehicles, and the next stages progressively move into fully autonomous terrain. Stage 4 can be compared to the auto-pilot mode in an airplane, while in Stage 5 we reach full automation with the driver having absolutely no responsibility during driving. These various stages along with the definitions and expected timelines for commercialization are highlighted in Fig. 2. Each of these stages require increasingly additional and more complex features that transfer more control from the driver to the truck.
Roland Berger recently analysed the implications of automated driving by assessing the required technology, costs, and benefits under various scenarios. We looked at the required content and technology needed to meet the various stages of automation, and then estimated the additional cost it would add to the overall vehicle. We then evaluated the potential cost savings expected by adoption of this technology and estimated the payback period under various scenarios for the fleet operator. The various technologies to be considered for autonomous trucks are shown in Fig. 3.
On mapping the cost across the various stages, we notice that most of the incremental cost is linked to software (75%) and it is no longer a hardware or product play. Especially in Stage 4 and 5, the value addition is mainly by software. As we move along the various stages, we see the cost progressively increasing and ultimately adding over US$ 20K to the vehicle cost, in effect making the truck significantly more expensive (Fig. 4).
In terms of benefits, the major positive impact is in stage 4 is where the driver can rest while the truck is driving, thereby clocking more miles, while in stage 5 we can even have a driverless vehicle. This reduces the largest operational cost head, viz., driver cost, especially in the developed nations. While this monetary impact may not be as high in developing nations, such as India, it nevertheless helps address the acute problem of driver availability and motivation which is increasingly a serious issue faced by fleet operators across the country.
In terms of fuel cost, which is another major cost block for both developed and developing countries alike, it offers opportunities in terms of platooning which ensures that the trucks run more efficiently. Platooning increases fuel efficiency for leading truck by 5% and trailing truck by 10%, thereby leading to overall team saving for the platoon of ~6%. This is substantial in the context of a fleet operator whose margins are always under pressure. Another area of cost saving is the repair and maintenance cost, due to better optimization in the way we use tryes, gearbox, etc. Additionally, there will also be a positive impact in terms of insurance cost due to better algorithms expected to lead to lesser accidents and thereby driving down insurance premiums significantly, especially in Stage 4 and 5. On the negative side, the additional equipment and software costs make it more expensive, and especially in Stage 1-3 there is no significant impact on driver costs.
We analysed several use cases for automated trucks – long haul, regional travel on high traffic roads, and regional travel with short distance traffic between regional hub and local warehouse. We observed that the per mile savings were low in all the above use cases up to Stage 3 after taking into account the increased equipment costs. Reduction in driver costs however drive savings in Stage 4 and 5, especially in long haul and regional high traffic roads. This indicates that it is not necessarily a positive business case for a fleet operator investing in this new technology, assuming platooning of less than 50%. There may be some specific applications which are more suited and run in geofenced locations, e.g., to and fro from an industrial zone to a harbour for transporting material. However, for regular operations we do not foresee a strong pull from customers currently as the payback period for Stage 2 and 3 are significantly higher (than a 3 year payback time which is typically considered reasonable). The situation however may change in Stage 4 and 5 automation, as mentioned earlier.
Several key challenges need to be addressed for automated driving, especially in the areas of technology, supply chain, legal requirements, ethical consideration, and an enabling ecosystem, as outlined in Fig. 5.
Multiple ecosystem requirements and stakeholder viewpoints therefore need to be addressed before automated trucks can become a market reality. The push from OEMs will remain limited as long as legal and cyber-security issues are not resolved. For existing OEMs this is yet another disruption in their business model and further raises questions on their role as system integrators and ability to capture a fair value in the commercial vehicle industry. There will also be limited pull from fleet operators as the financial upside is currently fairly limited. As a result, regulators would have to be the main drivers for autonomous trucks, whereby the need for higher safety requirements would push ADAS in the market and drive adoption of automated trucks.
Another key impact going forward would be changes in the roles and responsibilities in the value chain at different levels of automation, resulting in emergence of 2 types of OEMs – the technology-leader OEMs and the technology-follower OEMs. The technology-leader OEM will want to have complete system understanding, be able to integrate fail-operational vehicle safety concept and drive ADAS acceptance with regulators and customers. It would expect this technology to provide it with a better USP in the long run and serve as a differentiator vis-à-vis competition which will eventually enable it to charge a premium. The suppliers in such a system will need to have a holistic ADAS understanding from the components perspective (sensors and algorithms) to complete systems. They will have to work with OEMs to develop infrastructure (V2V, V2I). The technology-follower OEM, on the other hand, will be content with vehicle level integration and happy to live with a black box approach to some of the functionalities. In this case, the supplier will have to take the development lead for affordable and secure ADAS solutions and develop complete system competency, including sensors and software capabilities.
There would be new business models that would emerge, for example, Platoon Service Providers (PSPs) who will orchestrate platoon formation across fleets. They will provide intra-fleet services by matching trip schedules and coordinating / monitoring platoon formations, truck order, dis-engagements, and ensure that the benefits are fairly divided among all the participants. Large fleet operators will gain a competitive advantage due to high capability to platoon within their own fleet, thereby capturing this capability internally. At the same time, based on a recent study, they are also reasonably open to partner with other large fleets and more willing to wait for another truck in order to platoon and bring down fuel costs. If the owner operators do not follow suit then operating costs will come down for large fleet operators, which will translate into their gaining more market share at the expense of the owner operator who will end up losing market share.
In order to make automated trucking a reality, all the key stakeholders – fleet operators, OEMs, suppliers and Government – need to be fully engaged and work together. Fleet operators will need to investigate the individual benefits of investing into automated trucks. This would mean analyzing potential cost benefits of automated trucks based on characteristics of individual operations, and evaluating potentials to benefit from fuel cost savings through platooning either between own vehicles or with peers. For OEMs, the main task is to now prepare technologically for limited / full self-driving automation. They will need to further develop ADAS understanding on the vehicle and system level in-house to have relevant knowledge for designing limited / full self-driving trucks. They would also need to partition ADAS based on clearly defined interfaces and responsibilities to facilitate interaction with their supplier base. Suppliers, on the other hand, should ensure that their future focus encompasses both technology and business models. They should develop advanced software capabilities and introduce next generation sensor technologies to approach series production readiness for the stages of limited / full self-driving automation. They should also build effective business models for providing OEMs with both complete systems and ADAS components only, as per their specific needs. The Government has a very crucial role to play as it needs to provide the necessary legal framework that allows adoption of automated truck technology. For this, it needs to enable testing of automated trucks and clarify liability issues, as well as develop legal regulation for driverless truck operation in Stage 5.
While leading global OEMs and suppliers are already actively working in this area, it also opens up several opportunities for Indian players. Indian OEMs can already look at potential partnering opportunities with global OEMs and technology partners, so that they can be ahead of the curve. This will potentially help them become technology-leaders in the domestic market when the local ecosystem matures and adoption of technology improves for the various stages. Indian suppliers can leverage the global opportunity and manufacture cost effective sensors and equipment, which will drive down the additional cost of the vehicle, thereby improving the business case for fleet operators and help drive faster adoption. Organizations such as ARAI could support the development by setting up the necessary infrastructure and testing facilities for automated trucks. It could also help in coordination between the center and various states to set up a common legal and regulatory framework, based on study of global best practices and standards. Effective collaboration and pro-activeness by all the key participants will lead to faster progression of the technology, increase adoption and thereby lead to benefits to all the stakeholders concerned and the society in general.
By Jeffry Jacob, Partner, and Wilfried Aulbur, Senior Partner, Roland Berger